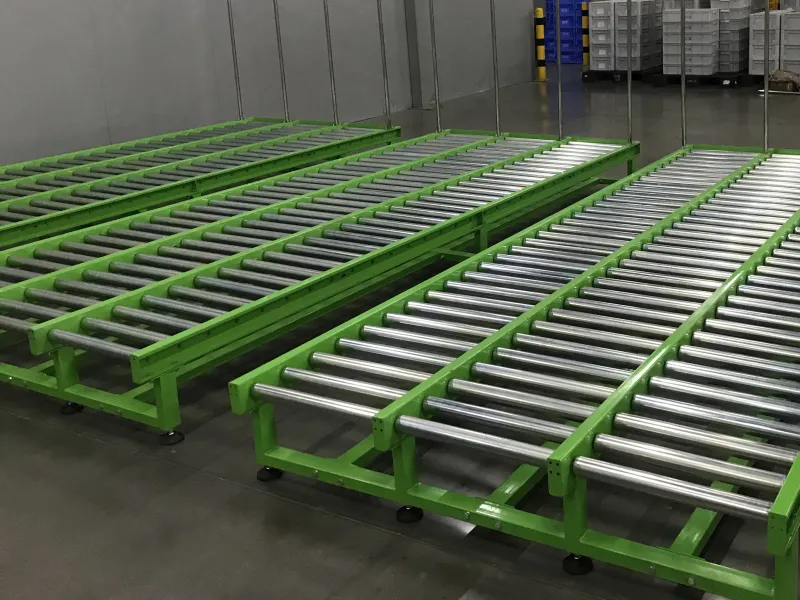
How to Choose a Unpowered Roller Conveyor?
Choosing an unpowered roller conveyor requires evaluating your specific application needs, material characteristics, facility constraints, and budget. Since unpowered roller conveyors rely on gravity or manual force to move items, they are simple, cost-effective solutions ideal for short-distance transport of stable, lightweight to medium-weight loads. Below is a step-by-step guide to help you select the right unpowered roller conveyor.
1. Define Your Application Requirements
- Purpose: Identify the conveyor's function (e.g., transport, staging, loading/unloading).
- Example: Moving boxes from a truck to a warehouse floor vs. staging totes in a picking area.
- Load Type: Determine the items to be transported (e.g., boxes, totes, lightweight pallets). Unpowered roller conveyors work best with flat-bottomed, stable items.
- Weight Capacity: Estimate the maximum weight per item (typically 50–500 lbs for light-duty, up to 1,000 lbs+ for medium-duty). Ensure the conveyor can handle your heaviest load without deformation.
2. Assess Material Characteristics
- Item Size and Shape: Measure the dimensions (length, width, height) of your items. Items must span at least three rollers for stability (e.g., a 12" long item needs rollers spaced 4" apart or less).
- Surface: Check if items have a smooth, flat base or are irregular/fragile. Smooth, stable bases are ideal; small, irregular, or soft items may require closer spacing or a belt conveyor.
- Weight Distribution: Ensure loads are evenly distributed to avoid tipping or stalling.
3. Determine Conveyor Specifications
- Width: Match the conveyor width to your widest item, adding a margin (e.g., 2–4 inches) for stability.
- Light-duty: 12"–24".
- Medium-duty: 24"–36".
- Length: Measure the distance items need to travel (e.g., 5–20 feet).
- Modular sections (e.g., 5' or 10' lengths) offer flexibility.
- Roller Spacing: Set spacing to support items securely (e.g., 2"–6" centers). Closer spacing (e.g., 2"–3") for smaller or lighter items; wider (e.g., 4"–6") for larger, stable loads.
- Incline Angle (if Gravity-Driven): Choose a slight decline (1–5°) based on load weight and desired speed. Light loads (e.g., 5 lbs) may need 3–5°; heavier loads (e.g., 50 lbs) may work with 1–2°.
- Flat Applications: Flat setups require manual pushing, best for short distances.
4. Select Roller Type and Material
Roller Diameter:
- 1.5"–1.9": Common for light-duty (up to 100–200 lbs), easier to start moving.
- 2.5" or larger: For heavier loads or wider items, offering more durability.
Roller Material
- Steel: Durable, cost-effective, for most industrial loads; galvanized or coated to resist rust.
- Plastic: Lightweight, corrosion-resistant, for delicate or light items.
- Aluminum: Balances strength and weight, good for portability.
Bearings
- Non-Precision: Basic, low-cost, for light loads or slow movement.
- Precision: Smoother, quieter, for heavier loads or frequent use.
5. Evaluate Facility Constraints
- Space: Measure available floor space and height difference (if inclined). For example, A 10' conveyor at 3° needs ~6" height drop; ensure clearance for the full length.
- Height: Set the conveyor at an ergonomic level (e.g., 30"–36" at the lower end) for loading/unloading.
- Adjustable legs or supports allow customization.
- Portability: Decide if it needs to be movable (e.g., with wheels or lightweight frame). Portable options suit temporary tasks like unloading.
- Layout: Confirm it fits with existing equipment or flows (e.g., feeding into a powered conveyor).
6. Choose Frame Material
- Steel: Strong, durable, for fixed installations; powder-coated for rust resistance.
- Aluminum: Lightweight, corrosion-resistant, easier to move or adjust.
Match to environment (e.g., stainless steel for washdown or food-grade areas).
7. Factor in Load Dynamics
- Gravity Flow and Manual Push Flow: Test the incline to ensure controlled speed.
- Too steep (e.g., >5°) causes runaway; too flat (<1°) stalls heavier items.
- Optional brakes or dampers can slow heavier loads.
- Manual Push (Flat Option): If no incline, confirm items move easily by hand.
- Best for light loads (<50 lbs) over short distances (<10 feet).
- Flow Control: Ensure items won't jam; side guides or wider spacing can help.
8. Safety and Ergonomics
- Safety Features: Include side rails or guards to prevent items from falling, especially on wider conveyors or inclines. End stops at the lower end stop items from rolling off.
- Operator Comfort: Set height and incline for easy access; avoid steep angles that strain workers or risk damage.
9. Budget and Long-Term Costs
- Initial Cost: Unpowered roller conveyors are affordable ($100–$1,000+), depending on size, material, and features. Steel is cheaper than aluminum; longer/wider units cost more.
- Operating Cost: Zero energy use, making it highly cost-effective.
- Maintenance: Minimal—inspect rollers and bearings periodically; choose durable materials to reduce wear.
10. Verify Standards and Test Options
- Regulations: Ensure compliance (e.g., OSHA for safety, FDA for food-grade if applicable).
- Stainless steel or coatings may be required.
- Supplier Input: Share load, size, and layout details with vendors (e.g., Ashland Conveyor, Grainger) for recommendations.
- Request a quote or sample layout.
- Testing: Test with your items to confirm smooth flow and stability, especially for varying weights or sizes.
Example Decision Process
- Scenario: A retail backroom needs to move 15-lb totes (18" x 12") from storage to a packing area, 8 feet away.
- Load: 15 lbs, light-duty suitable.
- Width: 20" (18" tote + margin).
- Length: 10' section (slightly longer for flexibility).
- Roller Spacing: 3" centers (tote spans 6 rollers).
- Incline: 2° (~4" drop over 10') for gentle flow.
- Rollers: 1.9" steel, non-precision bearings for cost.
- Frame: Aluminum, portable with wheels.
- Budget: Targets $400, prioritizing simplicity.
- Choice: A light-duty unpowered roller conveyor with steel rollers and adjustable supports.
Final Tips
- Test the Slope: Start shallow and adjust—too steep risks damage, too flat stops movement.
- Modular Option: Choose connectable sections for future changes.
- Compare Vendors: Get multiple quotes to optimize cost and quality.
By following these steps, you can select an unpowered roller conveyor that meets your needs efficiently and economically. If you have a specific scenario or need help with incline calculations, let me know!
Leave Me Your Requirement!