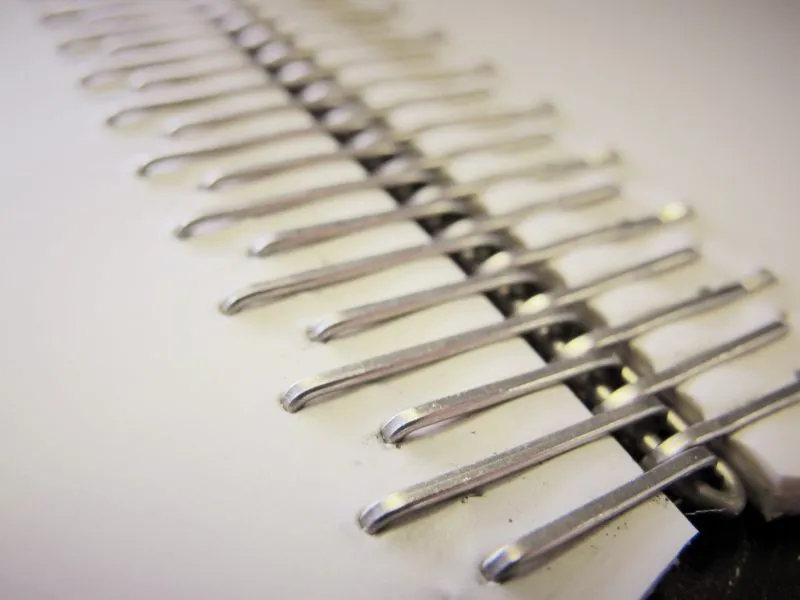
The Common Troubleshooting of Wire Hook Fastener
Although wire hook fastener splices are very reliable, there are times when a splice may not be performing to the user’s expectations. Following are some potential problems they may be facing:
Hooks Open Up and Release From Belt End
Possible Causes:
- Wrong size hook may have been selected.
- Tension may be too high for the strength of the hook.
- Hooks may be under-compressed.
- Belt may not be cut square.
- Belt may be mistracking.
Hooks Pull Through Belt End Without Opening Up
Possible Causes:
- Hooks may not be reaching back far enough into the belt.
- Wrong belt may have been selected.
- Belt end may not be cut square.
- Wrong size hook may have been selected.
- Hook may be too large for the minimum pulley.
Belt Fractures Directly Behind Fasteners
Possible Causes:
- Hook may be too large for the minimum pulley.
- Incorrect belt may have been selected.
- Wrong size hook may have been selected.
Step in the Lacing
Possible Causes:
- Incorrect installation procedures may have been used.
- Belt end may not be cut square.
Hooks Rust or Corrode
Possible Cause:
- Wrong hook material may have been selected.
Connecting Pin Fractures Prematurely
Possible Causes:
- Connecting pin may be too rigid for the application.
- Belt may be mistracking.
- Wrong connecting pin may have been selected.
Premature Connecting Pin Wear
Possible Causes:
- Wrong connecting pin may have been used. Consider a connecting pin with more resistance to abrasion.
Connecting Pin Difficult To Insert Into Splice
Possible Causes:
- Wrong connecting pin may have been selected.
- Pin may not be rigid enough. Consider using a solid core pin or a pin with a leader assembly.
- Belt Wave may be occurring. Consider switching wire hook.
- Hooks may be improperly installed.
Connecting Pin Migrates Out Of Splice:
Possible Causes:
- Belt end may not be cut square.
- Wrong pin material may have been selected.
- Smooth exterior of the pin might be allowing the pin to migrate out of the splice. Consider using notched steel or stainless pins.
- Pin may not be secure in the splice. Consider 'J End' pins.
Hook Legs Fracture Prematurely
Possible Causes:
- Hook size may exceed the recommended minimum pulley diameter.
- Hooks may have been over-compressed.
- Hooks may have been under-compressed.
A Flat Spot Is Worn On The Hook Knuckle
Possible Causes:
- Metal chosen for hook is not abrasion resistant enough for the application. Select a material that is more abrasion resistant (i.e. high tensile).
- Hooks may be under-compressed.
- Hooks may be over-compressed and have caused the knuckles to back out of the belt.
Premature Loop Wear
Possible Causes:
- Wrong connecting pin may have been selected.
- Connecting pin may need replacement.
- Metal chosen may not be abrasion resistant enough for the application. Select a material that is more abrasion resistant (i.e. high tensile).
- Hooks may be over-compressed, causing a "light bulb" loop shape.
Hook Loops Lean Together In Pairs
Possible Causes:
- Hooks may be under-compressed.
- May be using carded hooks. Consider using hooks, where each individual hook is welded to a common bar, keeping the hook legs parallel.
Hooks Twist
Possible Causes:
- Hooks may be over-compressed.
- Hook points may be too long for the belt thickness.
Splice Triggers Magnetic Detector
Possible Causes:
- Hook selected may be magnetic. Consider switching to a material without magnetic properties: Bronze, Hastelloy, or Inconel. 316 Stainless Steel is only slightly magnetic and can often be used.
Splice Triggers Metal Detector
Possible Cause:
- All hooks will trigger metal detectors. Consider switching to a non-metallic fastener such as Alligator Spiral or Alligator Plastic Rivet.
- Hook Points Twist (lay over) Instead of Properly
Penetrating Belt
Possible Causes:
- Belt may be too hard for the hook points to properly penetrate. Heat hook points or belt prior to installation.
- Hook points may be too long for the belt thickness.
End Hooks Pull Out Of Splice
Possible Causes:
- Lacing may be too close to the edges. Leave 1/4 -1/2" unlaced on both sides of the belt.
- Hooks may be under-compressed.
- Tension load may be too high for the strength of the hook. Consider a larger size hook, a hook made from a larger diameter wire, and/or a hook made from high tensile wire.
- Pin may be too short, allowing the splice to snag on obstructions.
Belt Wave
Possible Causes:
- Hooks may be over-compressed.
- Belt displacement may have occurred during the installation of the splice. Consider switching fasteners. The welded bar keeps the splice flat and eliminates the belt wave.
Leave Me Your Requirement!