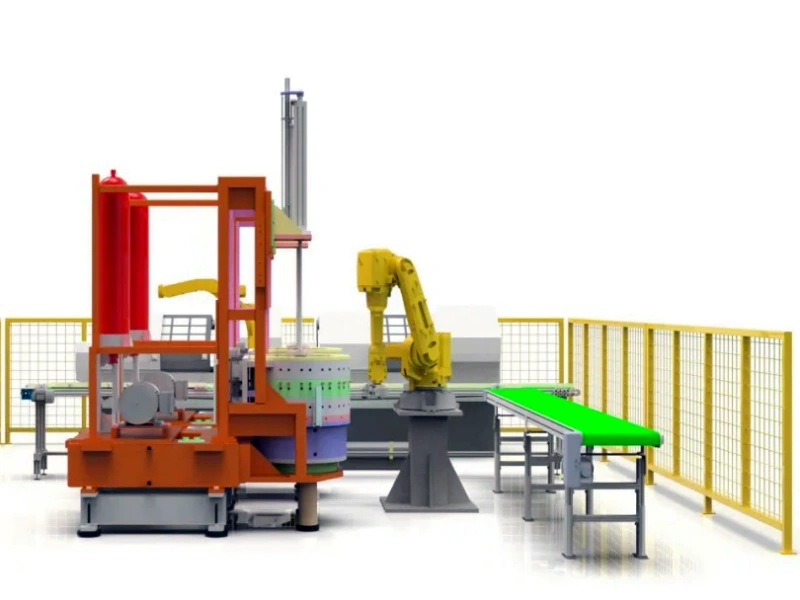
Conveyor Lightweight Structure Design and Optimization
Conveyors, as an indispensable part of logistics systems, have garnered increasing attention for structural optimization and lightweight design. This article explores the necessity of optimizing conveyor structures and the role of lightweight design in enhancing efficiency.
1. Necessity of Structural Optimization
As a key component of logistics systems, the structural design of belt conveyors and roller conveyors directly impacts production efficiency, energy consumption, and equipment lifespan. Poor structural design can lead to material accumulation, deviation, or even blockages, disrupting production processes. Structural optimization aims to enhance conveyor stability, reliability, and adaptability, catering to diverse material handling needs.
This is a telescopic belt conveyor for truck loading unloading system.
2. Importance of Lightweight Design
Lightweight design, a critical principle of modern engineering, focuses on reducing material usage to lower equipment weight. In conveyor design, this approach not only minimizes energy consumption and operational costs but also reduces resource dependency, aligning with sustainability goals. Benefits include:
- Energy Efficiency: Reduced weight leads to lower energy requirements during operation.
- Cost Reduction: Lightweight systems decrease transportation and installation costs.
- Environmental Impact: Less material usage contributes to sustainable development.
3. Practices in Structural Optimization and Lightweight Design
Material Selection and Strength Analysis
- Using high-strength, wear-resistant materials enhances conveyor durability while reducing maintenance costs.
- Advanced material choices can achieve lightweight designs without compromising performance.
Structural Simulation and Optimization
- Utilizing computer simulation technologies allows virtual testing of conveyor structures.
- Stress distribution and deformation analyses under various load conditions guide structural enhancements to ensure stability under high-load scenarios.
Reducing Friction Resistance
- Optimizing components like rollers and idlers minimizes friction resistance during material transfer.
- Lower friction reduces energy consumption and improves conveyor efficiency.
Integration of Intelligent Control Systems
- Intelligent control systems dynamically adjust conveyor speed and operation modes based on real-time material conditions.
- These systems further boost efficiency while minimizing unnecessary energy use.
This is a v belt dirving flexible roller conveyor system.
4. Case Study
At a logistics warehouse, structural optimization and lightweight design of its conveyor system resulted in smoother material transfer and significant energy savings. The movable truck loading unloading conveyors and telescopic belt conveyors will beneifits from the light design. Key improvements included:
- Material Optimization: Selecting advanced materials reduced equipment weight and enhanced durability.
- Structural Simulation: Simulations identified stress points and guided reinforcement where necessary.
- Intelligent Controls: Automated adjustments for different material types increased throughput and lowered operational costs.
The result was a system with reduced energy consumption, lower maintenance needs, and improved operational efficiency, saving substantial labor and material resources for the enterprise.
5. Future Prospects
With ongoing advancements in technology, conveyor structural optimization and lightweight design will find broader applications across industries. Innovations in material science and the development of more sophisticated control systems are expected to further enhance conveyor performance. Future trends may include:
- Advanced Materials: Greater adoption of lightweight, durable composites and alloys.
- Smart Systems: Enhanced AI-driven control mechanisms for adaptive and predictive system management.
- Sustainability Focus: More eco-friendly designs with reduced carbon footprints.
Structural optimization and lightweight design play a vital role in enhancing industrial production efficiency, reducing energy consumption, and achieving sustainable development. By adopting intelligent control systems, selecting advanced materials, and implementing simulation-driven design, conveyor systems can achieve high-performance operations.
As technology continues to evolve, conveyor innovation will bring greater value to industrial automation, setting new benchmarks for efficiency and sustainability in logistics and manufacturing.
Leave Me Your Requirement!