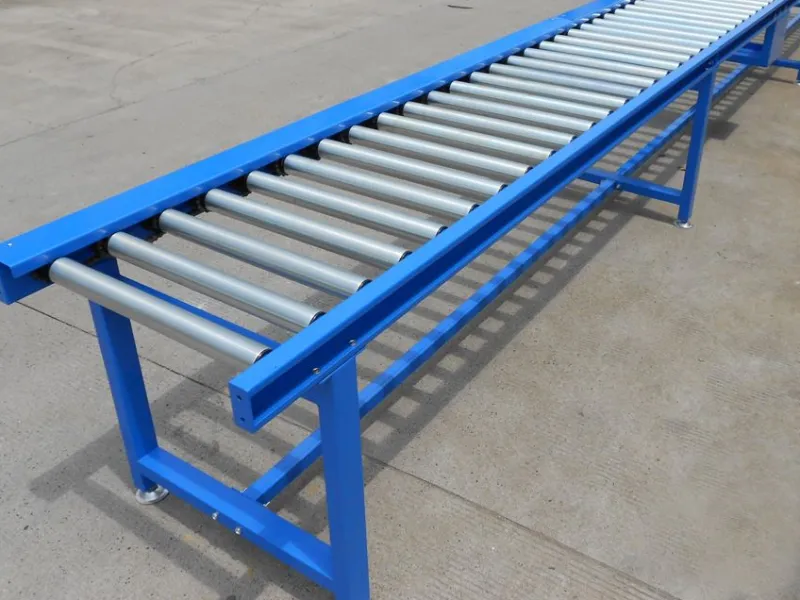
How to Choose a Gravity Roller Conveyor?
Choosing the right gravity roller conveyor involves assessing your operational needs, material characteristics, facility layout, and budget to ensure efficient, cost-effective material handling. Gravity roller conveyors rely on a slight incline or manual force to move items, making them simple and energy-free but requiring careful selection for optimal performance. Below is a step-by-step guide to help you choose the best gravity roller conveyor for your application.
1. Define Your Application Requirements
- Purpose: Determine the conveyor's role (e.g., transport, staging, unloading). For Example, Moving boxes from a truck to a sorting area vs. staging parts in an assembly line.
- Load Type: Identify the items to be transported (e.g., boxes, totes, lightweight pallets). Gravity roller conveyors work best with flat-bottomed, stable items.
- Weight Capacity: Estimate the maximum weight per item (typically 50–500 lbs for light-duty, up to 1,000 lbs+ for heavier-duty gravity systems). Ensure the conveyor supports your heaviest load.
2. Assess Material Characteristics
- Item Size and Shape: Measure the dimensions (length, width, height) of your items. Items must span at least three rollers for stability (e.g., a 12" long box needs rollers spaced 4" apart or less).
- Surface: Check if items have a smooth, flat base or are irregular/fragile. Smooth, stable items work best; small or irregular items may need closer roller spacing or a belt conveyor.
- Weight Distribution: Ensure loads are evenly distributed to prevent tipping or stalling.
This is a curved gravity roller conveyor system.
3. Determine Conveyor Specifications
- Width: Match the conveyor width to your widest item, adding a margin (e.g., 2–4 inches) for stability.
- Light-duty: 12"–24".
- Medium-duty: 24"–36".
- Length: Measure the distance items need to travel (e.g., 5–20 feet). Modular sections (e.g., 5' or 10' lengths) can be combined for flexibility.
- Roller Spacing: Set spacing to support items securely (e.g., 2"–6" centers). Closer spacing (e.g., 2"–3") for smaller or lighter items; wider (e.g., 4"–6") for larger, stable loads.
- Incline Angle: Choose a slight decline (1–5°) based on load weight and desired speed. Light loads (e.g., 5 lbs) may need 3–5°; heavier loads (e.g., 50 lbs) may work with 1–2°.
Test to avoid runaway speeds or insufficient movement.
4. Select Roller Type and Material
Roller Diameter:
- 1.5"–1.9": Common for light-duty (up to 100–200 lbs).
- 2.5" or larger: For heavier loads or wider items.
Larger diameters reduce effort needed to start movement.
Roller Material:
- Steel: Durable, for most industrial loads; galvanized or coated to resist rust.
- Plastic: Lightweight, corrosion-resistant, for delicate or light items.
- Aluminum: Balances strength and weight, good for portability.
- Bearings: Choose between non-precision (basic, low-cost) or precision (smoother, for heavier loads).
5. Evaluate Facility Constraints
- Space: Measure available floor space and height difference. Ensure room for the conveyor's length and incline (e.g., a 10' conveyor at 3° needs ~6" height drop).
- Height: Set the conveyor at an ergonomic level (e.g., 30"–36" at the lower end) for loading/unloading.
- Adjustable legs or supports allow customization of flexible gravity roller conveyor and normal gravity roller conveyor.
- Portability: Decide if it needs to be movable (e.g., with wheels or lightweight frame). Portable options suit temporary setups like truck unloading.
- Layout: Confirm it integrates with existing equipment or flows (e.g., feeding into another conveyor).
6. Consider Frame Material
- Steel: Strong, durable, for fixed installations; powder-coated for rust resistance.
- Aluminum: Lightweight, corrosion-resistant, easier to move or adjust.
Match to environment (e.g., stainless steel for washdown or food-grade areas).
These are gravity roller conveyor system.
7. Factor in Load Dynamics
- Speed Control: Gravity conveyors rely on the incline; test to ensure items move at a safe, controlled pace. Add optional brakes or speed dampers for heavier loads to prevent runaway.
- Flow: Ensure items won't jam or collide; wider spacing or side guides can help.
- Manual Push (Flat Option): If no incline is possible, confirm workers can push items easily (best for short distances, light loads).
8. Safety and Ergonomics
- Safety Features: Include side rails or guards to prevent items from falling, especially on wider conveyors. End stops at the lower end prevent items from rolling off.
- Operator Comfort: Set height and incline for easy loading/unloading; avoid steep angles that strain workers or damage goods.
9. Budget and Long-Term Costs
- Initial Cost: Gravity roller conveyors are affordable ($100–$1,000+), depending on size, material, and features. Steel is cheaper than aluminum; longer/wider units cost more.
- Operating Cost: Zero energy use, making it cost-effective long-term.
- Maintenance: Minimal—check rollers and bearings periodically for wear; choose durable materials to reduce replacements.
10. Verify Standards and Test Options
- Regulations: Ensure compliance (e.g., OSHA for safety, FDA for food-grade if needed).
- Stainless steel or specific coatings may be required.
- Supplier Input: Share load, size, and layout details with vendors (e.g., Ashland Conveyor, Hytrol) for recommendations.
- Request a quote or CAD design.
- Testing: Test with your items to confirm smooth flow and stability, especially if weights or sizes vary.
Example Decision Process
- Scenario: A small warehouse needs to move 20-lb boxes (15" x 12") from a dock to a sorting table, 10 feet away.
- Load: 20 lbs, light-duty suitable.
- Width: 18" (12" wide box + margin).
- Length: 10' straight section.
- Roller Spacing: 3" centers (box spans 5 rollers).
- Incline: 2° (~4" drop over 10') for controlled speed.
- Rollers: 1.9" steel, non-precision bearings for cost savings.
- Frame: Steel, fixed, with side rails.
- Budget: Targets $500, prioritizing simplicity.
- Choice: A basic gravity roller conveyor with steel rollers and adjustable legs.
Final Tips
- Test the Incline: Start with a shallow angle and adjust—too steep causes runaway, too flat stalls movement.
- Modular Design: Choose connectable sections for future expansion.
- Compare Vendors: Get multiple quotes to balance quality and cost.
By following these steps, you can select a gravity roller conveyor that meets your needs efficiently and economically. If you have a specific scenario or need help with roller spacing calculations, let me know!
Leave Me Your Requirement!