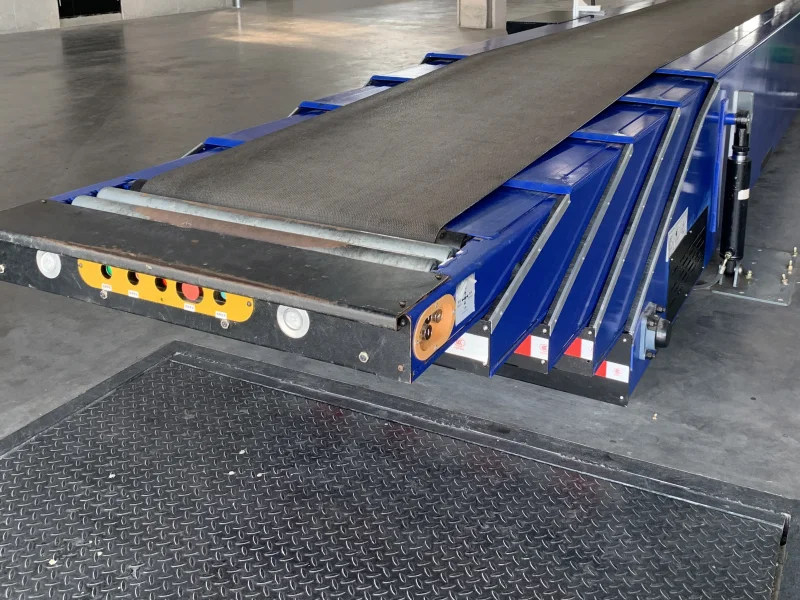
Durability & Life Prediction Design of Conveyors
In the vast framework of industrial production, conveyors undeniably play a pivotal role, bearing the critical task of material transportation. Their performance directly impacts production efficiency and operational costs. Therefore, when it comes to engineering design and conveyor selection, considerations regarding durability and lifespan prediction become particularly significant. These two factors act as "yardsticks" to measure whether a conveyor can reliably serve production processes over the long term. This article delves into the durability and lifespan prediction design of conveyors and analyzes actual cases to provide valuable references and guidance for engineers and decision-makers.
1. Understanding the Concept of Conveyor Durability
The durability of a conveyor essentially reflects its ability to maintain continuous and stable operation under specified working conditions. A durable conveyor requires minimal maintenance and rarely faces the replacement of critical components, ensuring smooth production activities. Various interrelated factors affect conveyor durability, collectively influencing its overall performance. Inbelts offer belt conveyors and roller conveyors for your project.
1.1 The Crucial Role of Material Selection
The construction materials of a conveyor form the foundation of its durability. These materials must possess sufficient strength to withstand the impacts generated during material transportation while exhibiting excellent wear resistance to counteract the damage caused by prolonged friction. Only then can the conveyor consistently operate in good condition, avoiding premature failures due to material deficiencies.
1.2 Precision Matching of Design Parameters
The design parameters of a conveyor act as a set of "operational guidelines" tailored specifically for it, with each parameter being crucial. For instance:
- Belt speed must balance material transport efficiency and operational stability.
- Load capacity should precisely align with the weight requirements of materials in actual production.
- Conveying distance should be determined based on the production layout.
When these design parameters perfectly match specific application requirements, the conveyor can operate stably within its capacity, avoiding decreased durability caused by overuse or improper application.
1.3 Maintenance as a Safeguard
Routine and standardized maintenance and inspection are indispensable for extending the lifespan of conveyors. Much like regular "check-ups" and "care" for equipment, promptly addressing potential issues, replacing worn-out components, and cleaning internal parts can ensure that the conveyor consistently operates in optimal condition. This prevents minor problems from escalating into major failures, effectively safeguarding its durability.
1.4 Environmental Factors and Their Impact
The environmental conditions in which a conveyor operates are an essential factor. Temperature fluctuations, humidity levels, and the presence of chemicals can directly affect a conveyor's durability. For example:
- High temperatures can accelerate material aging.
- High humidity environments can lead to rusting of components.
- Chemical substances may corrode surfaces, reducing overall performance and durability.
This is a telescopic belt conveyor for truck loading unloading.
2. Effective Methods for Predicting Conveyor Lifespan
To ensure long-term reliable operation in industrial production, accurately predicting a conveyor's lifespan is essential. The following methods provide scientific approaches to lifespan prediction from different perspectives.
2.1 Stress Analysis for Insight
Using professional engineering tools, such as finite element analysis, to analyze the stress and strain on critical conveyor components is a key means of lifespan prediction. Much like conducting a "stress test," this approach reveals the forces at play under different working conditions. Combined with the mechanical properties of materials, it helps estimate the operational lifespan of components and foresee potential failure points.
2.2 Material Studies for Lifespan Clarity
In-depth research into the materials used for conveyors is equally crucial. Experiments and analysis can determine fatigue characteristics and durability indices, providing a clear understanding of how material performance changes over time. This data serves as a basis for estimating the operational lifespan of conveyors built with these materials, offering scientific insights for subsequent maintenance and management.
2.3 Maintenance Records: Retrospect and Outlook
Detailed records of maintenance and repair activities contain valuable information. Analyzing historical maintenance data helps identify patterns in component failures, wear trends, and other key factors. By combining these patterns with current operational conditions, it becomes possible to predict a conveyor's future lifespan, providing strong support for preventive maintenance planning.
2.4 Real-Time Monitoring Systems
Installing advanced monitoring systems enables real-time tracking of a conveyor's operational and health status. Acting like a "smart stethoscope," such systems capture subtle changes during operation, such as abnormal temperature rises or increased vibration. They can promptly issue alerts for maintenance actions, while the collected data helps analyze performance trends, assisting in lifespan prediction.
3. Strategies for Enhancing Lifespan During Design
Taking scientifically sound measures during the initial design phase of a conveyor can significantly improve its lifespan. Below are several key aspects to consider:
3.1 Material Selection: Building a Strong Foundation
Choosing high-strength and wear-resistant materials is the primary step in extending a conveyor's lifespan. From belts and rollers to transmission components, each critical part should be carefully selected to ensure optimal performance in complex, long-term working conditions.
3.2 Structural Optimization: Balancing Stress
Reasonable structural design is key to ensuring durability. The design should account for the mechanical relationship between components, ensuring even stress distribution and avoiding stress concentration. For example, optimizing frame structures and improving connection methods can help evenly distribute forces, reducing fatigue damage risks and extending operational lifespan.
3.3 Maintenance Accessibility
Planning for sufficient maintenance space during design is an often-overlooked but crucial factor. Adequate space facilitates routine inspections, part replacements, and cleaning, ensuring timely maintenance and preventing issues from escalating, thereby extending lifespan.
3.4 Adherence to Standards
Ensuring that the conveyor design complies with relevant safety standards not only protects personnel during operation but also reduces maintenance costs and extends the equipment's lifespan. Adherence to standards minimizes risks of damage from accidents, enabling stable long-term operation.
3.5 Integrated Monitoring for Smart Management
Incorporating monitoring systems during the design phase equips conveyors with "smart sensing" capabilities, allowing them to provide real-time operational data. This enables proactive maintenance and significantly enhances overall lifespan through intelligent operational management.
Conveyor durability and lifespan prediction design are of paramount importance in industrial production. By focusing on material selection, structural design, maintenance, and monitoring, it is possible to effectively enhance conveyor lifespan, reduce operating costs, and improve production efficiency. Engineers and decision-makers should internalize these principles and flexibly apply them in design and operations to ensure long-term reliable performance, thereby creating greater value for their enterprises.
Leave Me Your Requirement!