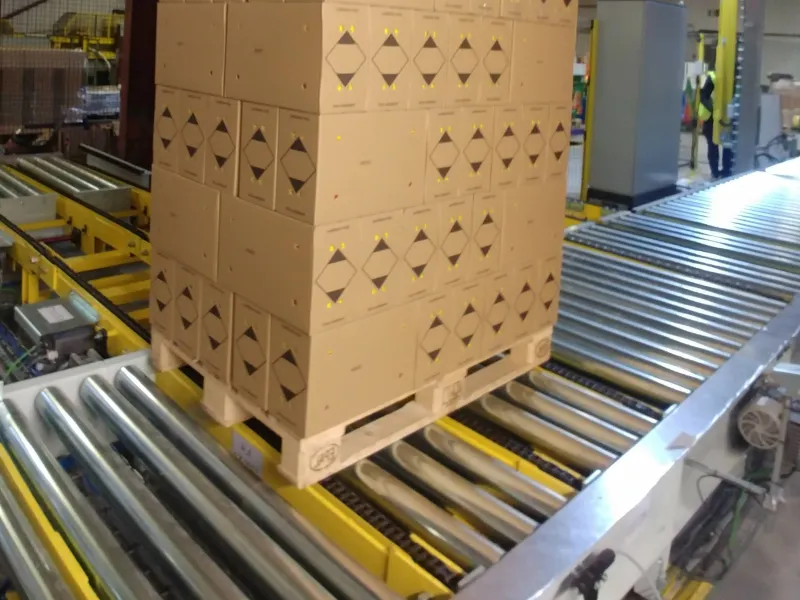
How to Choose a Pallet Roller Conveyor?
Choosing a pallet roller conveyor involves assessing your operational requirements, pallet characteristics, facility layout, and budget to ensure efficient, durable, and safe handling of palletized loads. These conveyors are designed for heavy-duty transport, typically handling pallets weighing 500–5,000 lbs or more. Below is a step-by-step guide to help you select the right pallet roller conveyor for your application.
1. Define Your Application Requirements
- Purpose: Identify the conveyor's role (e.g., transport, accumulation, staging, loading/unloading).
- Example: Moving pallets from a warehouse dock to storage vs. staging for production.
- Load Type: Confirm you're handling pallets (e.g., wooden, plastic, metal) and their contents. Pallet roller conveyors are optimized for flat-bottomed pallets.
- Weight Capacity: Estimate the maximum pallet weight, including contents (e.g., 1,000 lbs, 2,500 lbs). Include a safety margin (e.g., 20%) to avoid overloading.
2. Assess Pallet Characteristics
- Pallet Size: Measure dimensions (e.g., 40" x 48" standard North American pallet). Ensure the conveyor supports your largest pallet size.
- Pallet Condition: Check for damage, warping, or protruding nails. Damaged pallets may jam or require wider roller spacing.
- Bottom Surface: Verify the pallet's base (e.g., full bottom boards, runners). Must span at least three rollers; runners perpendicular to rollers need closer spacing.
- Load Stability: Assess if contents are stable or shift (e.g., stacked boxes, loose items). Unstable loads may need side guides or higher capacity.
Layout of Pallet Roller Conveyor System
3. Determine Conveyor Specifications
- Width: Match to your widest pallet, adding a margin (e.g., 4–6 inches).
- Example: 48" wide pallet + 6" = 54" conveyor width.
- Length: Measure the transport distance (e.g., 10–50 feet). Modular sections (e.g., 5' or 10' lengths) allow customization.
- Roller Spacing: Set to support pallets securely (e.g., 3"–6" centers). Closer spacing (e.g., 3"–4") for smaller or runner-based pallets; wider (e.g., 4"–6") for full-bottom pallets.
- Speed: Choose based on throughput (e.g., 30–60 ft/min for powered roller conveyor systems). Adjustable speed is ideal for varying workflows.
4. Select Drive Type
- Gravity-Fed: Uses a slight incline (1–3°) for movement. Our gravity roller conveyors are best for short distances, lighter pallets (<1,000 lbs), and low-cost applications.
- Limited control: requires height adjustment.
- Powered: Motor-driven rollers for consistent movement.
- Chain-Driven: Chains link rollers; robust, ideal for heavy pallets (1,000–5,000 lbs).
- Motorized Rollers: Internal motors (e.g., 24V DC or 110V); precise, quieter, for lighter pallets or automation.
- Line Shaft: Shaft with bands; less common for pallets due to lower torque. Motor power (e.g., 1–5 HP) matches load and speed.
5. Evaluate Facility Constraints
- Space: Measure floor space and ceiling height.
- Wide frames (e.g., 54"–60") and motors need clearance (e.g., 5–10 feet wide for heavy-duty).
- Layout: Decide if straight, curved, or transfer sections are needed.
- Curved sections use tapered rollers; transfers (e.g., turntables) redirect pallets.
- Height: Set for forklift/AGV access (e.g., 12"–24" low-profile) or ergonomic loading (e.g., 30"–36").
- Adjustable legs or fixed supports align with other systems.
- Power Supply: Confirm compatibility (e.g., 220V, 480V) for powered systems.
Pallet Roller Conveyor
6. Choose Roller and Frame Materials
Rollers
- Steel: Heavy-duty, for most pallets; galvanized or coated for rust resistance.
- Diameter: 2.5"–3.5" standard for pallets; larger (e.g., 4") for very heavy loads.
- Bearings: Precision or heavy-duty to handle weight and frequent use.
Frame
- Steel: Robust, durable, for fixed setups; powder-coated or galvanized.
- Match Environment: Stainless steel for washdown (e.g., food, cold storage).
7. Factor in Load Dynamics
- Accumulation: Decide if pallets need to queue.
- Zero-Pressure: Sensors stop rollers per zone; ideal for delicate or staged pallets.
- Low-Pressure: Rollers slip; suits sturdy pallets where slight contact is okay.
- Incline/Decline: For gravity, test angle (e.g., 1°–2°); for powered, ensure motor torque.
- Pallet Flow: Ensure smooth travel; damaged pallets or uneven loads may need wider spacing or guides.
8. Safety and Ergonomics
- Safety Features: Include emergency stops, guards, and load sensors.
- Side rails (e.g., 4"–6" high) prevent derailment; pallet stops manage flow.
- Operator/Forklift Access: Ensure height and clearance suit loading/unloading (e.g., 12"–18" for forklift forks).
- Low-profile designs integrate with AGVs or pallet trucks.
9. Budget and Long-Term Costs
- Initial Cost: Gravity: $500–$2,000; Powered: $3,000–$15,000+, based on size, drive, and features.
- Chain-driven is mid-range; motorized rollers are pricier but efficient.
- Operating Cost: Gravity has none; powered uses electricity—opt for energy-efficient motors.
- Maintenance: Gravity needs little; powered requires motor, chain, or roller upkeep—choose durable components.
Pallet Roller Conveyor
10. Verify Standards and Test Options
- Regulations: Ensure compliance (e.g., OSHA for safety, FDA for food-grade if applicable).
- Stainless steel or coatings may be required.
- Supplier Input: Share pallet size, weight, and layout with vendors (e.g., Hytrol, Dematic) for recommendations.
- Request a quote or CAD design.
- Testing: Test with your pallets to confirm stability, flow, and accumulation (if needed).
Example Decision Process
- Scenario: A warehouse needs to move 1,500-lb pallets (48" x 40") from a dock to storage, 20 feet away, with accumulation.
- Load: 1,500 lbs, heavy-duty.
- Width: 54" (48" pallet + 6" margin).
- Length: 20', with 2 zones (10' each, holds 2 pallets/zone).
- Drive: Chain-driven, 40 ft/min, 2 HP motor, zero-pressure accumulation.
- Rollers: 2.5" steel, 4" spacing (pallet spans 12 rollers).
- Frame: Steel, 18" height for forklift access, with 6" side rails.
- Budget: Targets $8,000, prioritizing durability.
- Choice: A powered pallet roller conveyor with chain drive, sensors, and heavy-duty rollers.
Final Tips
- Pallet Compatibility: Test with your exact pallet type—runners vs. full bottoms affect spacing.
- Scalability: Choose modular designs for future expansion.
- Compare Vendors: Get multiple quotes to balance cost and quality.
By following these steps, you can select a pallet roller conveyor that efficiently handles your loads while fitting your facility and budget. If you need help with a specific scenario or calculations (e.g., roller spacing), let me know!
Leave Me Your Requirement!