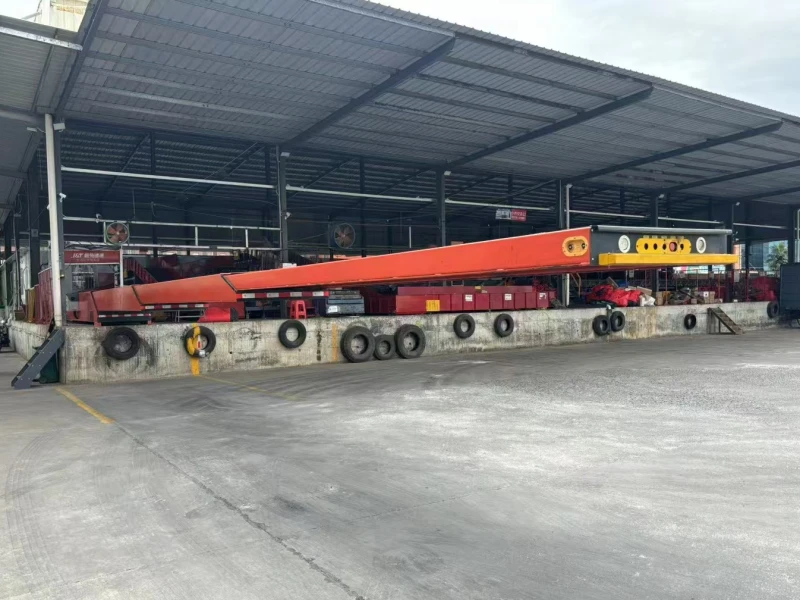
20ft and 40ft Containers Loading and Unloading Conveyor
20ft and 40ft Containers Loading and Unloading Conveyor is essential for modern logistics and supply chains. Container conveyors are specialized systems that streamline this process, offering speed, safety, and cost-saving benefits. This guide explores these systems in detail, helping you optimize your operations. Inbelts can supply belt conveyor and roller conveyor system for container loading unloading.
What is a Conveyor for 20ft and 40ft Containers?
A conveyor for 20ft and 40ft containers is a mechanical system designed to facilitate the movement of goods during the loading and unloading process. These systems typically include telescopic or flexible mechanisms that extend into containers, reducing the need for manual handling.
Importance of Container Loading/Unloading Conveyors
Loading and unloading containers manually is time-consuming and physically demanding. Conveyor systems improve efficiency by automating these processes, minimizing delays, and enhancing workplace safety.
These are portable telescopic belt conveyor for truck loading unloading.
Types of Conveyors for 20ft and 40ft Containers
1. Telescopic Conveyors
Telescopic conveyors are extendable systems that can reach deep into containers. Their adjustable length makes them ideal for handling 20ft and 40ft containers with precision and minimal labor.
2. Flexible Roller Conveyors
These flexible roller conveyors are portable and can be expanded or contracted as needed. They are particularly useful in tight spaces or for irregular loading operations.
3. Belt Conveyors
Belt conveyors provide a continuous surface for transporting goods. They are versatile and can handle various load types, including cartons, sacks, and pallets.
4. Truck Loading Dock Systems
Integrated dock systems combine conveyors with loading docks, offering a seamless solution for container operations. They are designed for high efficiency and durability in demanding environments.
This is a powered roller conveyor system.
Features of a Container Conveyor System
- Adjustable Length and Reach: Telescopic and flexible designs ensure the conveyor can adapt to different container sizes, providing optimal coverage for both 20ft and 40ft containers.
- Heavy-Duty Design: Container conveyors are built with robust materials to withstand the rigors of daily use in high-capacity operations.
- High Load Capacity: These systems can handle heavy and bulky loads, ensuring smooth movement and minimizing the risk of damage during transit.
Key Benefits of Using Loading and Unloading Conveyors
- Increased Efficiency: Conveyors significantly reduce loading and unloading times, boosting overall productivity and ensuring timely deliveries.
- Reduced Manual Labor: By automating material handling, conveyors alleviate the physical strain on workers, leading to lower labor costs and fewer injuries.
- Enhanced Safety Measures: Modern conveyors include safety features such as emergency stop buttons and protective barriers, creating a safer working environment.
Choosing the Right Conveyor for 20ft and 40ft Containers
- Space and Operational Requirements: Assess your loading dock's dimensions and workflow to select a conveyor system that fits seamlessly into your operations.
- Load Specifications: Consider the types of goods you handle, including their size, weight, and volume, to choose a system that meets your load requirements. The common loading capacity is 50kg/m and 100kg/m.
- Budget and Cost Analysis: While conveyors are an investment, their efficiency and long-term cost savings often justify the expense. Compare options to find the best value.
Installation Process for Container Conveyors
- Pre-Installation Planning: Evaluate your operational needs, dock layout, and integration requirements to prepare for a smooth installation process.
- Installation Steps: Professional technicians typically handle the installation, ensuring that the system is properly assembled, aligned, and connected to power sources.
- Testing and Optimization: Once installed, test the conveyor system to verify its functionality. Make adjustments as needed to optimize performance.
Maintenance of Loading and Unloading Conveyors
- Daily Inspections: Regularly check for wear and tear, misaligned belts, or other issues that could affect performance.
- Preventative Maintenance Routines: Schedule routine maintenance to address potential problems before they escalate, ensuring uninterrupted operations.
- Handling Repairs and Replacements: Keep spare parts on hand and have a plan for prompt repairs to minimize downtime.
These are telescopic conveyor working in a wharehouse.
Applications Across Industries
1. Logistics and Shipping
Conveyors are essential in shipping yards and warehouses for fast and efficient loading of containers.
2. Retail and E-commerce Warehousing
These systems help manage high volumes of goods, ensuring quick dispatch and delivery to customers.
3. Manufacturing and Distribution Centers
Conveyors streamline the movement of finished products from production lines to shipping containers.
Technological Advancements in Conveyor Systems
- Automation Integration: Modern conveyors can integrate with automated systems, such as robotic arms and guided vehicles, to enhance workflow.
- IoT and Smart Conveyors: IoT-enabled systems provide real-time monitoring and data insights, allowing for proactive maintenance and performance optimization.
- Energy-Efficient Solutions: Energy-saving motors and controls help reduce operational costs and support sustainability initiatives.
Common Challenges and How to Overcome Them
- Handling Irregular Loads: Adjustable conveyors can accommodate varying load sizes, ensuring smooth operations despite irregularities.
- Space Constraints in Loading Docks: Flexible and compact conveyor designs can maximize efficiency in confined spaces.
- Equipment Downtime Issues: Implementing predictive maintenance and having backup systems can minimize disruptions caused by equipment failure.
Safety Practices for Conveyor Systems
- Employee Training Programs: Ensure workers understand how to operate conveyor systems safely and recognize potential hazards.
- Implementing Emergency Stop Mechanisms: Equip conveyors with accessible emergency stop buttons to quickly halt operations if needed.
- Using Protective Equipment: Encourage the use of gloves, safety shoes, and other gear to prevent injuries during loading and unloading.
Future Trends in Container Conveyor Systems
- Robotics and AI in Logistics: Advanced robotics and AI algorithms are enabling smarter, more adaptive conveyor systems for container operations.
- Predictive Maintenance Technologies: Data-driven maintenance strategies predict and prevent issues before they occur, enhancing system reliability.
- Modular Conveyor Designs: Modular designs offer flexibility, allowing businesses to scale or reconfigure systems as needed.
FAQs about Containers Loading Unloading
1. What are the key features of a conveyor for 20ft and 40ft containers?
Key features include adjustable length, heavy-duty construction, and high load capacity to handle diverse goods efficiently.
2. How does a telescopic conveyor work for container loading?
A telescopic conveyor extends and retracts to reach into containers, allowing for seamless loading and unloading with minimal effort.
3. Are conveyor systems customizable for different container sizes?
Yes, many conveyors are adjustable and customizable to fit 20ft and 40ft containers, as well as other sizes.
4. What safety features should I look for in a conveyor system?
Look for emergency stop buttons, protective barriers, and anti-slip surfaces to ensure a safe working environment.
5. How do conveyors improve the loading and unloading process?
They automate material handling, reducing manual labor, speeding up processes, and improving accuracy and safety.
6. What is the average cost of installing such a system?
Costs vary based on system type, features, and complexity, but the long-term benefits often outweigh the initial investment.
Leave Me Your Requirement!