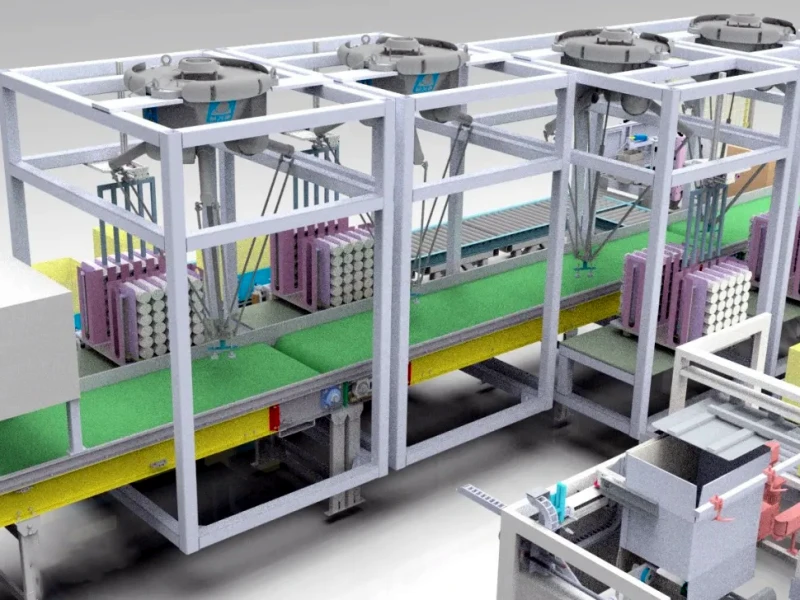
Detachable & Modular Design Conveyors
In today's industrial and logistics sectors, conveyors play an indispensable role in material handling across industries such as mining, ports, chemicals, food processing, and pharmaceuticals. To meet evolving production demands, conveyor designs continue to innovate, with detachable and modular designs emerging as pivotal advancements.
Detachable Design: Convenience and Diverse Benefits
Detachable designs enable easy disassembly and assembly of conveyor components, offering significant advantages in maintenance, repair, and upgrades.
1. Cost Efficiency
With detachable designs, only the malfunctioning components need to be replaced during breakdowns, eliminating the need for extensive repairs on the entire system. This significantly reduces maintenance costs and minimizes resource waste.
2. Improved Maintenance Efficiency
Detachable parts are easy to access and replace, allowing maintenance personnel to swiftly address issues and restore operations. This minimizes downtime, enhancing equipment utilization and reducing production delays.
3. Ease of Storage and Transportation
When not in use, detachable conveyors can be disassembled to save storage space. During transportation, their compact form makes them easier to handle and relocate, providing flexibility for warehouse management and on-site setup.
4. Facilitates Upgrades
Detachable designs support targeted upgrades by replacing specific components without overhauling the entire system. This not only lowers upgrade costs but also maximizes the reuse of the existing framework, promoting resource efficiency.
Key Considerations for Detachable Design
- Standardized Interfaces: Adopting universal standards like ISO ensures compatibility between parts, simplifying replacements and avoiding compatibility issues.
- Streamlined Disassembly Procedures: Clear and efficient disassembly protocols reduce operational complexity, allowing maintenance teams to work efficiently while minimizing risks of improper handling.
- Optimized Component Structures: Simplifying component designs and reducing the number of fasteners enhances ease of assembly and disassembly, saving time while improving reliability and stability.
This is portable telescopic belt conveyor for truck loading unloading.
Modular Design: Flexibility and Comprehensive Benefits
Modular design divides conveyors into independent functional modules, which can be rearranged to achieve diverse operational requirements.
1. Enhanced Flexibility
Modular designs enable conveyors to adapt to various production scenarios by combining and configuring modules as needed. Adjustments in conveying distance, speed, or material type are easily achieved through module reconfiguration, meeting a wide range of demands.
2. Reduced R&D Costs
By reusing existing modules in innovative combinations, manufacturers can quickly develop new conveyor systems without starting from scratch. This accelerates product updates, reduces development costs, and speeds up market entry.
3. Ease of Maintenance and Upgrades
When a module malfunctions, only the affected module needs replacement, simplifying maintenance and reducing costs. Equipment upgrades can also be achieved by improving or replacing specific modules, enhancing overall performance.
4. Shortened Production Cycles
Modular designs streamline production processes. Different modules can be manufactured simultaneously and assembled efficiently, boosting production speed and ensuring timely product delivery.
Key Considerations for Modular Design
- Rational Module Division: Modules should be clearly defined based on the conveyor's functional architecture and practical requirements, ensuring seamless integration and operation.
- Standardized Connections: Employing universal connection methods, such as bolts or pins, ensures module compatibility and simplifies assembly or replacement.
- Continuous Module Optimization: Simplifying module structures and reducing internal connections improve manufacturing efficiency and ease of use, contributing to reliable and efficient operations.
These are belt conveyor system for material tranferring.
Case Studies of Detachable and Modular Conveyor Designs
Case 1: Lightweight Conveyor for Logistics Distribution Centers
1. Background
A large e-commerce distribution center needed a conveyor system capable of handling a variety of packages while frequently adjusting layouts to accommodate changes in business operations, such as seasonal promotions or new warehouse zones. Inbelts can offer belt conveyor and roller conveyor system for logistic centers.
2. Application of Detachable Design
The conveyor belts featured detachable quick-release connections, enabling easy removal of worn or damaged sections. This reduced belt replacement time from several hours to just 30 minutes, significantly improving maintenance efficiency. Additionally, the detachable design facilitated swift reassembly in new warehouse zones, saving labor and time.
3. Application of Modular Design
The conveyor system was divided into modules such as feeding, sorting, conveying, and discharging. Sorting modules were further customized for different package types. For instance:
- A high-speed sorting conveyor for small parcels.
- A mechanical-arm-based module for large packages.
During peak seasons like Black Friday, additional feeding and conveying modules could be quickly integrated to handle increased package volumes. The telescopic belt conveyor is often working with modular design conveyor system. This modular setup reduced system development time by 40% as most modules were reused.
Case 2: Conveyors in the Food Processing Industry
1. Background
A food processing company needed conveyors to transport raw materials and finished goods while meeting strict hygiene standards. Frequent adjustments were also required to accommodate various product types and processes.
2. Application of Detachable Design
Detachable food-grade conveyor belts allowed for easy removal and thorough cleaning after transporting sticky products. This ensured compliance with hygiene regulations and reduced risks of contamination. Maintenance efficiency improved by 50% as faulty parts were easily replaced without dismantling the entire conveyor. The truck loading conveyor can be modular design in food processing factory.
3. Application of Modular Design
- The conveyor was divided into modules for raw material handling, cleaning, processing, and packaging.
- Different module combinations catered to varying product lines, such as cookies or candies.
- Adding a coating module enabled new product development.
- This modular approach reduced R&D costs by 40% and allowed the company to adapt quickly to market demands and regulatory changes.
Detachable and modular conveyor designs are essential for improving operational efficiency, adaptability, and cost-effectiveness. Detachable designs offer advantages in maintenance, storage, and upgrades, while modular designs provide unmatched flexibility, rapid development, and streamlined maintenance. Together, they represent a forward-thinking approach that ensures conveyors remain at the forefront of industrial and logistics innovation, supporting industries in achieving sustainable and efficient production.
Leave Me Your Requirement!