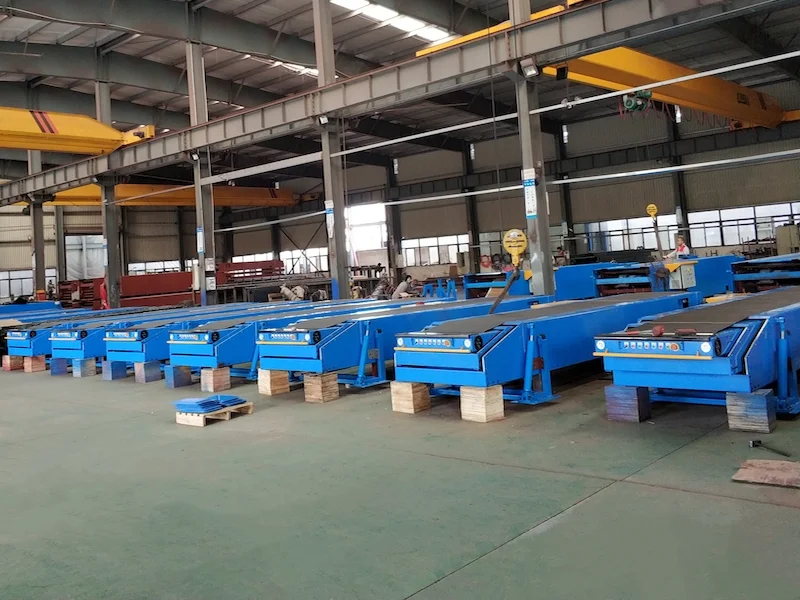
Intelligent Monitoring and Data Analysis Applications for Conveyors
As one of the essential components in modern industrial production, the conveyor's stable and efficient operation is crucial to the smooth functioning of production lines. To improve upon traditional manual inspection methods, intelligent monitoring and data analysis technologies have emerged. This article will explore the technical principles, key functions, and profound impact of intelligent monitoring and data analysis applications for conveyors in enhancing operational efficiency.
I. Intelligent Monitoring in Conveyor Systems
- Sensor Technology Application: By installing sensors, key parameters such as conveyor speed, temperature, and vibration can be monitored in real time, enabling continuous monitoring and early warnings for operational status. This allows for the early detection of potential issues and reduces the risk of breakdowns.
- Computer Vision Technology Application: Leveraging computer vision technology, the conveyor's operational state can be monitored through image recognition and analysis. This enables automatic detection and alerts for abnormal conditions, such as equipment malfunctions or foreign object blockages, enhancing detection accuracy and efficiency.
- Sound Recognition Technology Application: Acoustic sensors monitor and analyze the conveyor's sound signals in real time, detecting unusual noises and mechanical faults, which enables early warnings and fault diagnostics, thereby reducing the risk of equipment damage.
II. The Role of Data Analysis in Conveyor Systems
- Real-Time Data Collection and Analysis: Data collected in real time by intelligent monitoring devices undergoes data cleansing, processing, and analysis to extract critical information. This provides an accurate assessment of equipment operating status, helping optimize scheduling and maintenance plans.
- Fault Prediction and Diagnosis: Using machine learning and data mining technologies, historical data undergoes pattern recognition and anomaly detection to create predictive models that forecast potential faults. In-depth analysis and diagnosis provide targeted solutions.
- Operational Optimization and Energy Efficiency: By analyzing large volumes of operational data, bottlenecks and peak energy consumption periods within the roller conveyor and belt conveyor system can be identified, leading to optimized operating methods, energy-saving measures, and scheduling, thereby reducing energy usage and production costs.
III. Benefits of Intelligent Monitoring and Data Analysis Applications
- Increased Equipment Reliability and Safety: Real-time monitoring and fault prediction enable the timely detection and resolution of equipment anomalies, reducing downtime and production losses, and improving equipment reliability and operational safety.
- Precision Maintenance and Management: Relying on data analysis, tailored maintenance plans and service schedules can be developed, allowing for early detection of equipment degradation and fault indicators, lowering maintenance costs and repair times.
- Enhanced Operational Efficiency and Production Capacity: Data analysis helps optimize equipment scheduling and task sequencing, increasing conveyor efficiency and boosting the overall operational performance and capacity of the production line.
- Intelligent Decision Support: Based on data analysis results, decision support tools can be provided to help managers make informed and rational decisions, enhancing the company's competitiveness.
The application of intelligent monitoring and data analysis technology has made conveyor system monitoring and management more intelligent and efficient. Through real-time monitoring, data analysis, and predictive intelligence, equipment anomalies can be identified and resolved promptly, preventing faults and enhancing the stable, continuous operation of production lines.
Intelligent monitoring and data analysis have become key to improving conveyor performance. With intelligent monitoring technology, conveyors can be monitored in real time, and early warnings can be issued to detect equipment faults and abnormalities in advance. Data analysis, through advanced algorithms and models, provides decision support and optimization strategies for equipment operation and maintenance, increasing reliability and production efficiency. In the future, with ongoing advancements, intelligent monitoring and data analysis applications in the conveyor field will become even more comprehensive, creating greater value and competitive advantages for enterprises.
Leave Me Your Requirement!