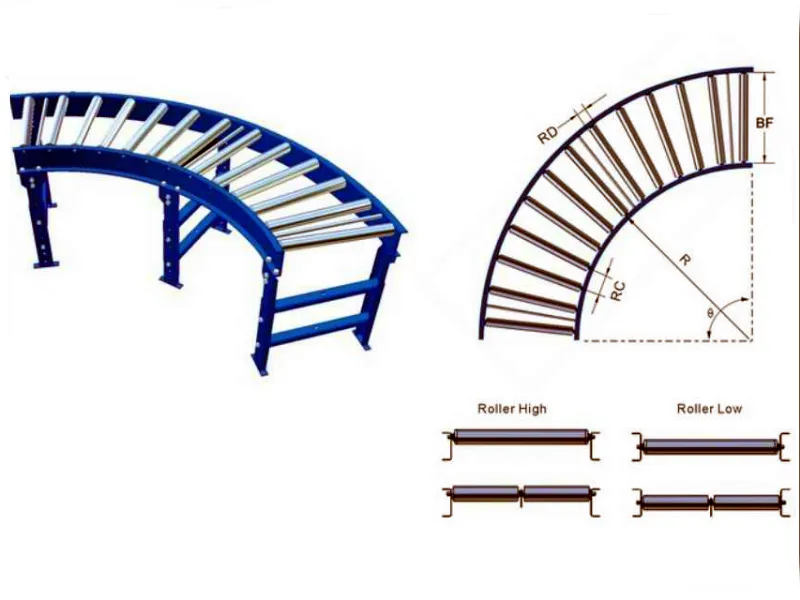
Curved Roller Conveyor Design
Designing a curved roller conveyor requires careful planning to ensure efficient material flow, proper load handling, and seamless integration into your facility. Unlike straight conveyors, curved roller conveyors must account for directional changes, speed differentials, and stability around bends. Below is a detailed guide on the key design considerations and steps for creating an effective curved roller conveyor, tailored for both gravity-fed and powered systems.
Key Design Considerations
1. Curve Angle
- Options: Common angles are 30°, 45°, 90°, or 180°, depending on the layout.
- Purpose: Determines how sharply the conveyor redirects items (e.g., 90° for a right-angle turn).
- Design Tip: Smaller angles (e.g., 30°–45°) are gentler on loads; sharper angles (e.g., 90°–180°) save space but may require more robust support.
2. Inner and Outer Radius
- Inner Radius: The tightest part of the curve (e.g., 18"–48"), dictating the conveyor's footprint.
- Outer Radius: Calculated as inner radius plus conveyor width (e.g., 18" inner + 24" width = 42" outer).
- Design Tip: Larger radii handle wider or less stable items but need more space; smaller radii are compact but limit load size.
3. Conveyor Width
- Range: Typically 12"–48", based on the widest item plus a margin (e.g., 2–4 inches) for stability.
- Design Tip: Ensure width accommodates the load while fitting the facility layout.
4. Roller Design
- Tapered Rollers: Essential for curves; wider at the outer edge, narrower at the inner edge to maintain smooth flow.
- Taper ensures consistent speed across the width despite the outer edge moving faster.
- Diameter: 1.5"–1.9" for light-duty (up to 200 lbs); 2.5" or larger for heavier loads.
- Material: Steel for durability; plastic for light or delicate items; aluminum for a balance of strength and weight.
5. Roller Spacing
- Rule: Items must span at least three rollers (e.g., a 12" long item needs 4" spacing or less).
- Range: 2"–6" centers; closer for small/light loads, wider for large/stable loads.
- Design Tip: Tight spacing prevents tipping but increases roller count and cost.
6. Frame Design
- Material: Steel for strength; aluminum for lightweight portability; stainless steel for washdown environments.
- Structure: Curved to match the radius, with cross-bracing for stability under load.
- Height: Typically 24"–36" (adjustable legs recommended for alignment with other systems).
7. Drive Mechanism
Gravity-Fed:
- Requires a slight incline (1–5°) to move items; angle depends on load weight and friction.
- Simple, no power needed, but limited control.
Powered:
- Line Shaft: Shaft under rollers with bands; cost-effective, light to medium loads.
- Chain-Driven: Chains link rollers; durable, for heavier loads.
- Motorized Rollers: Internal motors (e.g., 24V DC); precise, quiet, energy-efficient.
Motor placement (e.g., under frame) and power (e.g., 1/2–1 HP) match load and speed needs.
8. Speed Differential
- Challenge: The outer edge travels faster than the inner edge (e.g., a 90° curve with 24" inner radius has a longer outer path).
- Solution: Tapered rollers compensate; side guides or guards stabilize items prone to shifting.
9. Load Capacity
- Range: Light-duty (up to 200 lbs); medium-duty (200–1,000 lbs); heavy-duty (1,000 lbs+).
- Design Tip: Reinforce frame and rollers for heavier loads; check bearing ratings.
10. Safety and Support Features
- Side Guides/Rails: Prevent items from falling off, especially on sharp curves or with unstable loads.
- End Stops: For gravity systems, stop items at the curve's end.
- Guards: Cover moving parts (e.g., chains, motors) for operator safety.
Design Steps
1. Analyze Requirements
- Define load (size, weight, type), curve angle, and purpose (e.g., 90° turn for 20-lb boxes).
- Measure available space (e.g., 5' x 5' area for a 90° curve).
2. Calculate Dimensions
- Width: Widest item + margin (e.g., 12" box + 4" = 16" wide).
- Radius: Minimum inner radius based on space and load (e.g., 24" for a 16" wide conveyor).
- Arc Length: Use the formula: Arc Length = (π × Radius × Angle) / 180°
- Example: 90° curve, 24" radius = (3.14 × 24 × 90) / 180 = 37.7" arc length (inner edge).
3. Select Roller Specifications
- Diameter: 1.9" for 20-lb boxes.
- Spacing: 3" centers (12" box spans 4 rollers).
- Taper: Gradual taper (e.g., 1.9" inner to 2.5" outer) for smooth flow.
4. Choose Drive Type
- Gravity: 2° incline (~4" drop over 10') for light loads.
- Powered: Motorized rollers with 50 ft/min speed for control.
5. Design Frame
- Steel frame, 16" wide, 24" inner radius, 40" outer radius (16" + 24").
- Adjustable legs (24"–36" height) for alignment.
6. Incorporate Features
- Side guides (2" high) for stability.
- End stop for gravity; sensors for powered accumulation.
7. Validate Load Dynamics
- Test stability around the curve—ensure items don't tip due to speed differential.
- Adjust roller taper or add guides if needed.
8. Finalize and Prototype
- Create a CAD drawing or sketch (e.g., 90° curve, 16" wide, 24" radius).
- Build a small prototype or simulate with supplier software to confirm flow.
Example Design
- Scenario: A warehouse needs a 90° curved roller conveyor to redirect 20-lb boxes (12" x 10") around a corner.
- Angle: 90°.
- Width: 16" (12" box + 4" margin).
- Inner Radius: 24" (fits space; outer radius = 40").
- Rollers: 1.9" steel, tapered (1.9" inner to 2.5" outer), 3" spacing.
- Drive: Powered, chain-driven, 40 ft/min, 1/2 HP motor.
- Frame: Steel, 30" height, with side guides.
- Load Capacity: 50 lbs max (with safety margin).
- Features: Sensors for accumulation, emergency stop.
Design Tips
- Tapered Rollers: Critical for smooth turns; calculate taper based on radius and width.
- Test Flow: Prototype with your items to ensure stability and speed.
- Modularity: Design with standard sections for easy expansion or replacement.
- Supplier Tools: Use vendor design software for precision.
A well-designed curved roller conveyor balances functionality, space, and load requirements, ensuring efficient material handling. If you need help with calculations (e.g., arc length, taper angle) or a specific design scenario, let me know!
Leave Me Your Requirement!