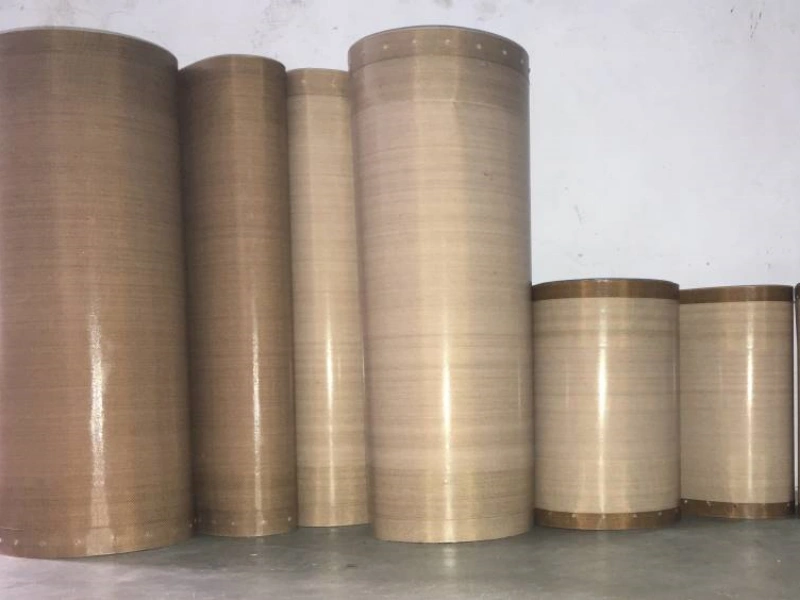
Industrial High-Temperature Conveyor Belt
In industrial production and logistics, conveyor belts are indispensable equipment widely used in high-temperature environments. However, traditional conveyor belt materials are prone to expansion, deformation, and strength reduction under high temperatures, affecting production efficiency and equipment lifespan. Therefore, selecting suitable heat-resistant conveyor belt materials is crucial. This article explores the challenges of high-temperature environments, material selection, and application cases.
Challenges for Conveyor Belts in High-Temperature Environments
Conveyor belts in high-temperature environments face several challenges, including:
- Material Expansion and Deformation: Increased temperature causes conventional materials to expand, reducing conveyor belt stability.
- Strength Reduction: High temperatures weaken mechanical properties, increasing the risk of breakage and damage.
- Reduced Wear Resistance: Materials conveyed in high-temperature conditions may cause additional wear on the conveyor belt.
- Chemical Reactions: High-temperature environments may lead to chemical reactions between the conveyor belt material and transported materials, affecting its service life.
To address these issues, selecting conveyor belt materials with excellent heat resistance is essential.
Selection of High-Temperature Conveyor Belt Materials
Different high-temperature environments require different types of conveyor belt materials. Below are some common heat-resistant conveyor belt materials and their characteristics:
1. Polytetrafluoroethylene (PTFE) Conveyor Belt
Temperature Range: -200°C to +260°C
Characteristics:
- Low friction coefficient, reducing wear
- High chemical stability, resistant to acid and alkali corrosion
- Excellent electrical insulation, suitable for the electronics industry
Application Fields: Food processing, semiconductor manufacturing, chemical industry
2. Polyimide (PI) Conveyor Belt
Temperature Range: Up to 300°C+
Characteristics:
- Excellent mechanical properties, resistant to stretching and tearing
- Strong corrosion resistance, suitable for harsh environments
- Maintains stability under high temperatures
Application Fields: Refining, metal processing, aerospace
3. Metal Conveyor Belt (Stainless Steel/Nickel Alloy/Titanium Alloy)
Temperature Range: Up to 1000°C+
Characteristics:
- Suitable for extreme high-temperature environments
- High strength and rigidity, ideal for heavy-load material transport
- Corrosion-resistant, suitable for high-temperature chemical environments
Application Fields: Steel smelting, coal processing, glass manufacturing
4. Silicone Rubber Conveyor Belt
Temperature Range: -60°C to +200°C
Characteristics:
- Good elasticity and flexibility
- Suitable for complex-shaped conveyor applications
- Resistant to chemical corrosion, applicable to certain special environments
Application Fields: Food processing, pharmaceutical industry, glass manufacturing
Comparison of Heat-Resistant Materials
The table below provides a comparison of different materials based on heat resistance, characteristics, and applications:
Material | Maximum Heat Resistance | Key Features | Typical Applications |
PTFE (Polytetrafluoroethylene) | 260°C | Low friction, chemical resistance | Electronics, semiconductors, food transport |
PI (Polyimide) | 300°C+ | High strength, heat-resistant | Refining, metal processing |
Metal Conveyor Belt (Stainless Steel) | 1000°C+ | Extreme heat resistance | Coal, metallurgy, glass manufacturing |
Silicone Rubber | 200°C | Flexible, high-temperature resistant | Glass production, food processing |
Key Factors in Selecting Heat-Resistant Materials
When choosing high-temperature conveyor belt materials, consider the following key factors:
- Temperature Adaptability: Ensure the conveyor belt remains stable at the operating temperature.
- Wear Resistance: Reduce long-term operational wear and extend service life.
- Chemical Stability: Resistant to acids, alkalis, and oxidizing agents.
- Strength Requirements: Provide sufficient tensile strength and tear resistance.
- Lifespan and Cost: Balance durability and cost-effectiveness to select the best solution.
Application Cases
1. Glass Production Industry
- Challenge: The temperature in glass production reaches up to 1200°C, causing traditional rubber conveyor belts to melt or degrade.
- Solution: Using silicone rubber conveyor belts ensures flexibility and stability under high temperatures, reducing downtime and improving production efficiency.
2. Metal Heat Treatment Industry
- Challenge: Conveyor belts must withstand high temperatures and strong oxidation environments during metal heat treatment.
- Solution: Stainless steel conveyor belts operate above 1000°C, resisting high-temperature oxidation and ensuring continuous production.
3. Refining Industry
- Challenge: High-temperature and high-pressure crude oil transport requires conveyor belts to endure extreme conditions.
- Solution: Polyimide conveyor belts provide heat resistance and corrosion resistance, making them suitable for demanding industrial environments.
Selecting appropriate high-temperature conveyor belt materials is crucial for production efficiency and equipment lifespan. In different industries, the right conveyor belt materials can reduce equipment wear, lower maintenance costs, and enhance efficiency. Therefore, companies should consider factors such as temperature range, wear resistance, chemical stability, strength, and lifespan when making selections to ensure optimal performance. In the future, advancements in material technology—such as nanocoating technology, ceramic composite materials, and intelligent monitoring systems—will further improve the performance of high-temperature conveyor belts, providing more reliable solutions for industrial production.
Leave Me Your Requirement!