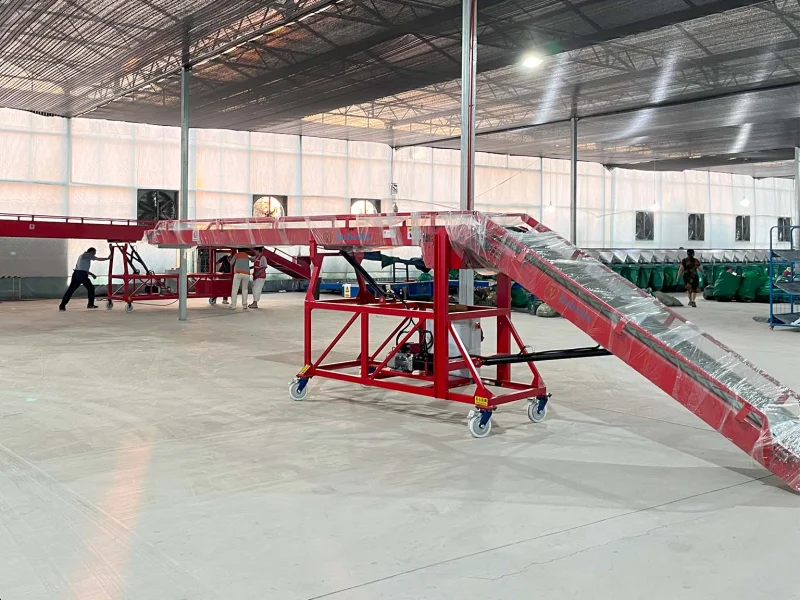
Bag Stacking Conveyor for Warehouse Management
In modern warehousing, where efficiency, space optimization, and labor savings are paramount, bag stacking conveyors play a critical role in streamlining the handling, transport, and stacking of bagged materials such as grains, sugar, cement, fertilizers, or chemicals. These specialized conveyor systems, designed for bags typically weighing 25–100 kg, automate the process of moving bags from trucks or filling stations to organized stacks in warehouses, reducing manual labor and enhancing operational productivity. With modular designs, adjustable heights, and robust construction, bag stacking conveyors are ideal for warehouses, distribution centers, and industries like agriculture, food processing, and manufacturing.
What is a Bag Stacking Conveyor?
A bag stacking conveyor is a material handling system engineered to transport and stack bags (e.g., jute, HDPE, PP, or paper sacks) in warehouses or godowns. These conveyors move bags from a loading point (e.g., truck or filling station) to a stacking area, often at adjustable heights from floor level to 2–12 meters (6.5–40 feet), where operators or automated systems arrange them into organized stacks for storage. Available in mobile, fixed, or telescopic configurations, bag stacking conveyors use belts, rollers, or chains to handle bags efficiently, with features like hydraulic height adjustment and automation for seamless integration into warehouse workflows.
Key Features of Bag Stacking Conveyors
- Load Capacity: Handles bags of 25–100 kg (up to 200 kg for heavy-duty models).
- Height Adjustability: Manual or hydraulic systems for stacking heights from 2–12 meters.
- Mobility: Mobile units with wheels or towbars for easy repositioning.
- Automation: Supports integration with sensors, PLCs, or robotic palletizers for automated stacking.
- Applications: Warehousing, agriculture, food processing, cement, and logistics.
Types of Bag Stacking Conveyors
Bag stacking conveyors come in various configurations to suit warehouse needs, from manual gravity systems to fully automated solutions. Below are the primary types used in warehouse applications:
1. Mobile Bag Stacking Conveyors
- Description: Portable belt or roller conveyors mounted on wheeled chassis, often with hydraulic or manual height adjustment for stacking bags up to 12 meters high.
- Specifications:
- Belt: Chevron or rough-top PVC/rubber, 600–800 mm wide, for grip on inclines (up to 20°).
- Length: 6–12 meters (20–40 feet); telescopic models extend up to 3:1 ratio.
- Load Capacity: 25–100 kg per bag; up to 600–1,200 bags/hour.
- Motor: 1–3 HP, 220V–400V, with geared motor for smooth operation.
- Best For: Flexible warehouse setups, loading/unloading trucks, or stacking in godowns.
- Pros: Mobile, adjustable height, reduces labor (e.g., 3 workers for 10 bags/min).
- Cons: Limited automation, moderate capacity ($3,000–$10,000 per unit).
- Example: Inbelts Mobile Bag Stacker with chevron belt for 50 kg grain bags.
2. Fixed Bag Stacking Conveyors
- Description: Stationary belt or chain-driven conveyors integrated into warehouse layouts for continuous stacking operations.
- Specifications:
- Belt/Chain: Flat or chevron belt (600–1,000 mm wide); drag chain for heavier bags.
- Length: 5–20 meters; fixed or modular sections.
- Load Capacity: 50–200 kg per bag; up to 1,000–2,000 bags/hour with automation.
- Motor: 2–5 HP, 400V, with PLC for automation.
- Best For: High-volume stacking in fixed warehouse zones or with robotic palletizers.
- Pros: High throughput, supports automation, durable.
- Cons: Less flexible, higher setup cost ($5,000–$20,000 per unit).
- Example: Prime Precisions Horizontal Bag Stacker with drag chain.
3. Telescopic Bag Stacking Conveyors
- Description: Extendable telescopic belt conveyors (e.g., 10–30 meters) with hydraulic height adjustment for stacking or loading/unloading.
- Specifications:
- Belt: Chevron PVC/rubber, 600–800 mm wide, for incline grip.
- Extension: 2:1–3:1 ratio (e.g., 10–30 meters).
- Load Capacity: 25–100 kg per bag; 600–1,500 bags/hour.
- Motor: 2–4 HP, 400V, with variable speed (10–30 m/min).
- Best For: Dynamic warehouse spaces, truck loading, or high stacks (up to 12 meters).
- Pros: Adjustable length/height, high efficiency, mobile options.
- Cons: Complex maintenance, higher cost ($6,000–$30,000 per unit).
- Example: Sautec Telescopic Bag Stacker with 600 mm rubber belt.
4. Roller Bag Stacking Conveyors
- Description: Gravity or powered roller conveyors for lighter bags (25–50 kg), often used with manual or semi-automated stacking.
- Specifications:
- Rollers: 1.5"–2.5" diameter, steel or plastic, 2"–4" spacing.
- Length: 5–10 meters per section.
- Load Capacity: 25–100 kg per bag; 200–600 bags/hour (gravity), 600–1,200 (powered).
- Motor (Powered): 1/4–1 HP, 24V–400V.
- Best For: Small to medium warehouses, short runs, or manual stacking.
- Pros: Low cost (gravity: $300–$1,500 per 10’), simple maintenance.
- Cons: Limited for heavy bags or automation.
- Example: Royal Conveyors Roller System for robotic bag stacking.
5. Automated Bag Stacking Conveyors
- Description: Belt or chain conveyors with sensors, PLCs, or robotic palletizers for fully automated stacking onto pallets.
- Specifications:
- Belt/Chain: Chevron belt or drag chain, 600–1,200 mm wide.
- Load Capacity: 25–100 kg per bag; up to 2,000–3,000 bags/hour.
- Controls: PLC, sensors, or robotic arms; 220V–440V, 3-phase.
- Best For: High-throughput warehouses or integration with bagging/palletizing systems.
- Pros: High automation, minimal labor, precise stacking.
- Cons: High cost ($10,000–$50,000+ per system), complex setup.
- Example: Tracey Packaging Dual-Station Palletizer with conveyor.
Benefits of Bag Stacking Conveyors
- Labor Savings: Reduces manpower (e.g., 3 workers for 10 bags/min vs. 10+ manually).
- Efficiency: Automates stacking, increasing throughput (600–3,000 bags/hour).
- Space Optimization: Stacks bags up to 12 meters, maximizing vertical storage.
- Safety: Minimizes manual lifting, reducing injury risks with safety features like emergency stops.
- Versatility: Handles various bag types (jute, HDPE, PP) and integrates with existing systems.
Applications of Bag Stacking Conveyors
- Stockpiling: Stacking bags (e.g., rice, sugar, cement) in organized piles up to 12 meters high for efficient storage.
- Loading/Unloading: Moving bags from trucks to warehouse stacks or vice versa, reducing manual handling.
- Packaging Lines: Transporting filled bags from bagging stations to stacking or palletizing areas.
- Agriculture: Handling seeds, grains, or fertilizers with precision to avoid damage.
- Logistics: Sorting and stacking bags for distribution or export in ports or warehouses.
Design Considerations for Bag Stacking Conveyors
Bag Specifications
- Size: E.g., 500 x 300 mm (sugar bags) to 800 x 500 mm (cement bags).
- Weight: 25–100 kg; heavy-duty models for 100–200 kg.
- Material: Jute, HDPE, PP, or paper; chevron belts for slippery bags.
- Base: Flat bases suit rollers; irregular bases need belts.
Throughput and Speed
- Manual: 200–600 bags/hour (gravity or semi-automated).
- Automated: 600–3,000 bags/hour (powered with sensors or robotics).
- Speed: 10–30 m/min, adjustable for production pace.
Stacking Height and Layout
- Height: 2–12 meters (floor to ceiling); hydraulic for high stacks.
- Layout: Straight, inclined (10–20°), or telescopic for truck loading.
- Space: Telescopic or mobile units for tight warehouse spaces.
Environment Protection
- Dry/Indoor: Mild steel or aluminum for grains, sugar, or fertilizers.
- Food-Grade: Stainless steel, sealed bearings for flour or cocoa.
- Outdoor: Galvanized or coated frames for cement or aggregates.
Automation Needs
- Manual: Gravity or mobile conveyors for small warehouses.
- Automated: Powered belts/chains with sensors or robotic palletizers for high-volume operations.
Safety Features
- Emergency stop buttons and safety interlocks.
- Protective barriers or guards for moving parts.
- Non-slip chevron belts for inclined transport.
- Stable chassis with lockable wheels for mobile units.
Bag stacking conveyors are vital for efficient warehouse operations, automating the handling and stacking of 25–100 kg bags of grains, sugar, cement, or other materials. With mobile ($3,000–$10,000), fixed ($5,000–$20,000), telescopic ($6,000–$30,000), or automated ($10,000–$50,000+) options, these conveyors cater to diverse needs, from small godowns to high-throughput distribution centers. Key features like chevron belts, hydraulic height adjustment, and automation ensure labor savings, high throughput (up to 3,000 bags/hour), and space optimization.
Leave Me Your Requirement!