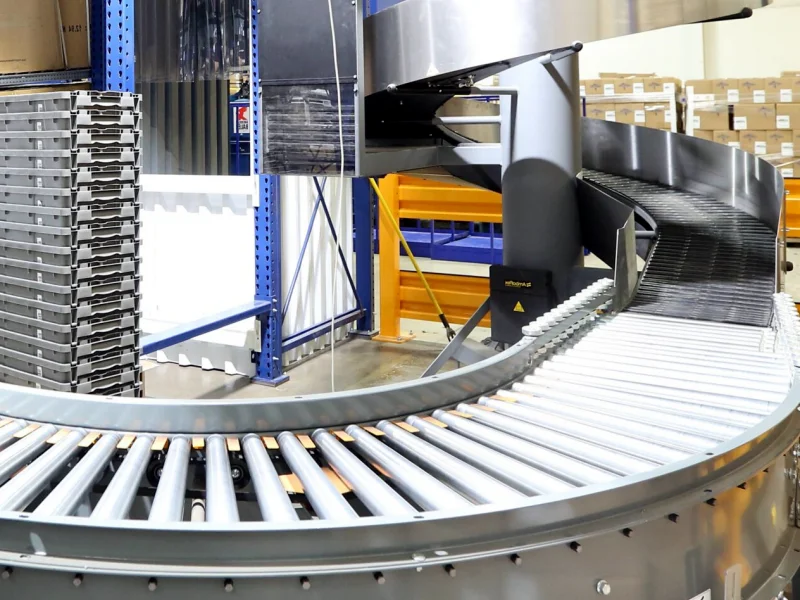
How to Choose a Accumulation Roller Conveyor?
Choosing an accumulation roller conveyor requires careful evaluation of your operational needs, material characteristics, facility layout, and budget. These conveyors are designed to allow items to stop and queue (accumulate) without pressure or damage, making them ideal for buffering, sorting, or staging in automated systems. Below is a step-by-step guide to help you select the right accumulation roller conveyor for your application.
1. Define Your Application Requirements
- Purpose: Identify why accumulation is needed (e.g., buffering between processes, staging for packing, sorting).
- Example: Queuing packages before shipping vs. holding parts for assembly.
- Load Type: Determine the items to be transported (e.g., boxes, totes, trays). Accumulation conveyors work best with flat-bottomed, stable items.
- Weight Capacity: Estimate the maximum weight per item or total load (e.g., 50–1,000 lbs+). Ensure the conveyor supports your heaviest load during accumulation.
2. Assess Material Characteristics
- Item Size and Shape: Measure dimensions (length, width, height). Items must span at least three rollers for stability (e.g., a 12" long item needs 4" spacing or less).
- Surface: Check if items are smooth, rough, fragile, or deformable. Fragile or soft items need zero-pressure accumulation to avoid damage.
- Weight Distribution: Ensure even distribution to prevent tipping or uneven pressure during queuing.
This is a roller conveyor system using chain and motor drive system.
3. Choose Accumulation Type
Zero-Pressure Accumulation (ZPA)
- Rollers stop in zones when items are detected (via sensors), preventing contact between loads.
- Best for fragile, delicate, or high-value items (e.g., electronics, glassware).
Low-Pressure Accumulation
- Rollers slip or slow under load, allowing slight contact pressure.
- Suitable for sturdy items (e.g., cardboard boxes, plastic totes) where minor pressure is acceptable.
Design Tip
ZPA is more expensive but safer for sensitive loads; low-pressure is simpler and cheaper.
4. Determine Conveyor Specifications
- Width: Match to your widest item, adding a margin (e.g., 2–4 inches) for stability.
- Light-duty: 12"–24"; heavy-duty: 24"–48".
- Length: Measure the total distance, factoring in accumulation zones (e.g., 10–50 feet). Each zone is typically 2–5 feet long, depending on item size.
- Roller Spacing: Set to support items securely (e.g., 2"–6" centers). Closer spacing for small/light loads; wider for large/stable loads.
- Speed: Select based on throughput (e.g., 30–150 ft/min). Variable speed allows flexibility; ensure it syncs with upstream/downstream processes.
5. Select Drive and Control System
Drive Mechanism:
- Motorized Rollers: Internal motors (e.g., 24V DC) per zone; quiet, precise, energy-efficient.
- Line Shaft: Shaft with bands drives rollers; cost-effective, good for light to medium loads.
- Chain-Driven: Chains link rollers; robust, for heavier loads or harsh conditions.
Control System:
- Sensors: Photoelectric or proximity sensors detect items and trigger zone stops (essential for ZPA).
- PLCs: Programmable logic controllers manage multiple zones and integrate with automation.
- Pneumatic: Air pressure controls roller brakes (less common, simpler).
- Power: Match motor to load and speed (e.g., 1/2 HP for light-duty, 1–3 HP for heavier loads).
6. Evaluate Facility Constraints
Space
- Measure floor space and ceiling height.
- Account for control boxes, sensors, and clearance (e.g., 3–5 feet wide for heavy-duty).
- Zone length must fit item size and queue needs.
Layout
- Decide if straight, curved, or inclined sections are needed.
- Curved accumulation requires tapered rollers and zoned control.
Height
- Set at an ergonomic level (e.g., 30"–36") or match existing systems.
- Adjustable legs offer flexibility.
Power Supply
- Confirm compatibility (e.g., 110V, 220V, 480V).
This is accumulation roller conveyor with curved roller conveyor for turning transporting.
7. Choose Roller and Frame Materials
Rollers:
- Steel: Durable, for most loads; coated for rust resistance or grip.
- Plastic: Lightweight, for delicate items or corrosion resistance.
- Diameter: 1.5"–1.9" for light-duty; 2.5" or larger for heavier loads.
Frame:
- Steel: Strong, durable, for fixed setups; powder-coated for longevity.
- Aluminum: Lightweight, easier to adjust.
- Match to environment (e.g., stainless steel for washdown).
8. Factor in Load Dynamics
- Queue Capacity: Calculate how many items need to accumulate (e.g., 5 boxes at 12" each = 5’ zone). Design enough zones to handle peak loads.
- Flow Control: Ensure smooth release from accumulation (e.g., timed or sensor-triggered). Avoid bottlenecks downstream.
- Pressure: Zero-pressure for no contact; low-pressure if slight pressure is tolerable.
9. Safety and Ergonomics
- Safety Features: Include emergency stops, guards, and sensors to prevent jams or overflows.
- Side rails keep items on track; roller covers reduce pinch risks.
- Operator Comfort: Set height and access for easy loading/unloading; minimize noise with quieter drives (e.g., motorized rollers).
10. Budget and Long-Term Costs
- Initial Cost: Ranges from $2,000–$10,000+, depending on length, drive, and controls.
- ZPA with motorized rollers is pricier; low-pressure line shaft is cheaper.
- Operating Cost: Factor in electricity; energy-efficient motors (e.g., 24V DC) save money.
- Maintenance: Motors, sensors, and drives need regular checks; choose durable, accessible designs.
11. Verify Standards and Test Options
- Regulations: Ensure compliance (e.g., OSHA for safety, FDA for food-grade if needed).
- Stainless steel or coatings may be required.
- Supplier Input: Share load, speed, and accumulation needs with vendors (e.g., Hytrol, Interroll) for advice.
- Request a quote or CAD layout.
- Testing: Test with your items to confirm stability, accumulation, and release timing.
Example Decision Process
- Scenario: A packaging line needs to queue 10-lb boxes (12" x 10") before a sealing machine, 15 feet away.
- Load: 10 lbs, light-duty.
- Width: 16" (12" box + margin).
- Length: 15’, with 3 zones (5’ each, holds 4 boxes/zone).
- Type: Zero-pressure accumulation (fragile boxes).
- Drive: Motorized rollers (24V DC), 40 ft/min, sensor-controlled.
- Rollers: 1.9" steel, 3" spacing.
- Frame: Steel, 30" height, with side guides.
- Budget: Targets $5,000, prioritizing precision.
- Choice: A ZPA roller conveyor with motorized rollers and PLC controls.
Final Tips
- Match Accumulation Type: Choose ZPA for fragile items, low-pressure for sturdy loads.
- Zone Planning: Design enough zones for peak demand; test flow.
- Compare Vendors: Get multiple quotes to optimize cost and features.
By following these steps, you can select an accumulation roller conveyor that meets your buffering needs efficiently and reliably. If you have a specific scenario or need help with zone sizing, let me know!
Leave Me Your Requirement!