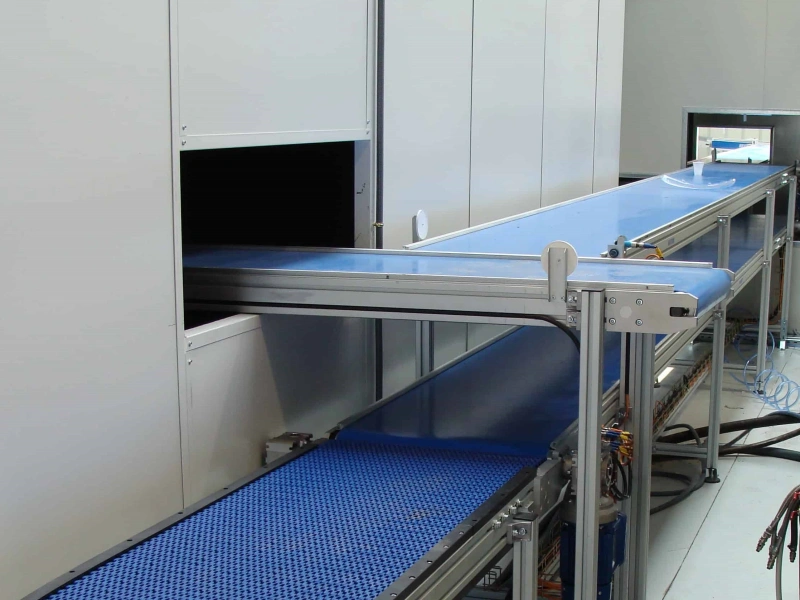
Mechanical Failure of Conveyor and Emergency Treatment Strategy
In today's rapidly advancing industrial automation landscape, conveyors serve as indispensable tools for material handling, playing a crucial role in production processes. However, given their prolonged and high-intensity operation, mechanical failures are inevitable.This article provides a comprehensive analysis of common conveyor mechanical failures and effective emergency handling strategies, offering robust support for addressing issues during production.
Analysis of Common Mechanical Failures
1. Pulley/Chain Breakage
Prolonged heavy-load operation can lead to conveyor pulley or chain breakage. When this occurs, the conveyor belt can no longer operate properly, severely disrupting the material transport process.
2. Transmission Component Failures
Key transmission components such as gearboxes and motors frequently encounter issues. For example, gears may suffer damage, or bearings may overheat due to excessive operation, adversely affecting the functionalityof telescopic belt conveyors in warehouse.
3. Belt Malfunctions
The conveyor belt, as the direct carrier of materials, is prone to issues such as slippage, breakage, or misalignment. These problems not only hinder material flow but can also cause blockages, potentially bringing the entire transport process to a standstill.
4. Guide System Malfunctions
Faults in the guide system can cause materials to deviate from their intended path, with severe cases leading to material spillage. This poses significant challenges to production efficiency.Guide rails can prevent falling of conveyors.
5. Loose Fasteners
Prolonged vibrations can loosen fasteners on the conveyor. When this happens, the stability of the entire system may be compromised, affecting both the equipment's operation and the smooth flow of materials.
Detailed Emergency Handling Strategies
1. Immediate Shutdown and Power Isolation
At the first sign of an anomaly, the primary and most critical step is to immediately stop the conveyor and disconnect its power supply. This measure prevents the issue from escalating and causing more severe consequences.
2. Inspection and Diagnosis
Skilled maintenance personnel should promptly conduct a thorough inspection of the affected components. Utilizing available instruments and diagnostic tools, they can accurately identify the root cause of the failure to guide subsequent repair actions.
3. Replacement of Spare Parts
If critical components, such as a broken conveyor belt or damaged transmission parts, are found to be faulty, they should be replaced immediately using spare parts. For example, replacing a broken belt or repairing/replacing faulty transmission components can restore the conveyor's normal operation.
4. Lubrication and Maintenance
Ensuring adequate lubrication for key components such as gears and bearings is essential for smooth operation. After emergency handling, comprehensive lubrication and maintenance should be performed to restore optimal working conditions and extend the equipment's service life.
5. Adjustment and Calibration
For issues such as belt misalignment or material buildup, timely adjustment and calibration of the guide system are necessary to ensure the conveyor remains in proper working condition, guaranteeing stable and efficient material transport.
6. Failure Logging and Analysis
Each failure incident should be meticulously documented, including details such as the time of occurrence, handling process, and affected components. These records can be used for subsequent analysis to draw lessons and prevent similar problems from reoccurring.
7. Training and Prevention
Regular training programs for maintenance personnel are essential to enhance their emergency handling skills. Additionally, periodic inspections and maintenance of equipment help identify and mitigate potential failure risks, reducing the likelihood of future issues.
Mechanical failures in conveyors can lead to significant disruptions in industrial production. However, with effective emergency handling strategies, downtime can be minimized, and production efficiency can be greatly improved. It is vital to prioritize the safety of maintenance personnel and strictly adhere to operational protocols throughout the fault-handling process.
Through continuous learning and experience accumulation, we can address various conveyor mechanical failures more effectively, ensuring stable and uninterrupted production activities.
Leave Me Your Requirement!