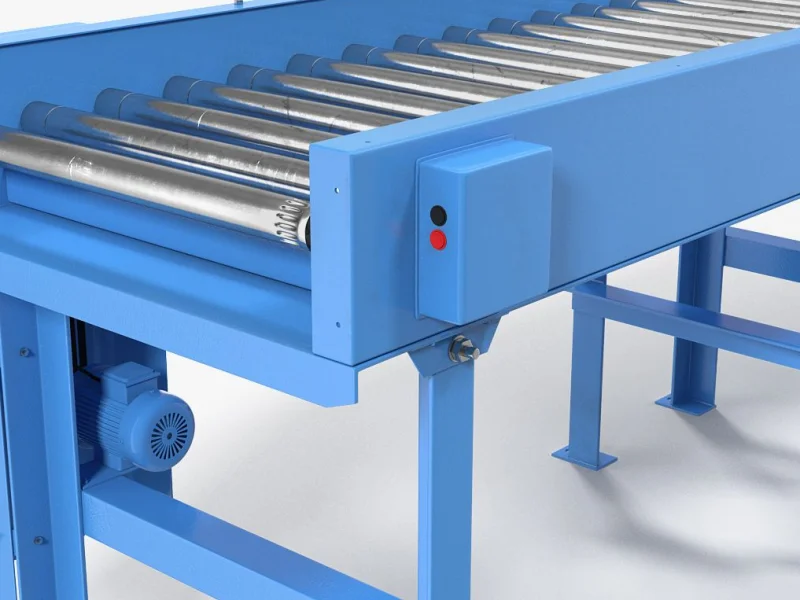
Roller Conveyor Side Rails for Operation Protection
Roller conveyor side rails are structural components attached to the sides of a roller conveyor to guide loads, prevent items from shifting or falling off, and enhance safety. They are particularly important for:
- Alignment: Keeping items (e.g., boxes, pallets, totes) centered on the conveyor, especially around curves or during high-speed operation.
- Safety: Protecting operators and preventing loads from derailing, especially for unstable or heavy items.
- Stability: Supporting items on inclines, declines, or during accumulation.
Side rails are used in all types of roller conveyors, including gravity, powered, chain-driven, accumulation, pallet, and curved systems.
Purpose of Roller Conveyor Side Rails
Prevent Load Derailment: Stop items from sliding off due to misalignment, curves, or external forces (e.g., forklift bumps).
- Guide Loads: Ensure consistent positioning for downstream processes (e.g., sorting, packing).
- Protect Operators: Reduce risks of items falling onto workers or walkways.
- Support Accumulation: Keep queued items aligned in accumulation conveyors.
- Enhance Stability: Critical for unstable loads (e.g., stacked boxes, loose items) or high-speed conveyors.
Types of Roller Conveyor Side Rails
1. Fixed Side Rails
- Description: Permanently attached to the conveyor frame via bolts or welds.
- Use Case: Stable, repetitive loads (e.g., pallets, uniform boxes).
- Height: 1"–6" (common: 2" for boxes, 4"–6" for pallets).
- Material: Steel, aluminum, or stainless steel.
- Pros: Durable, low maintenance.
- Cons: Less flexible for varying load sizes.
2. Adjustable Side Rails
- Description: Mounted on brackets or slots, allowing width or height adjustments.
- Use Case: Variable load sizes (e.g., mixed boxes, totes).
- Height: 1"–12" (adjustable via clamps or screws).
- Material: Steel or aluminum, sometimes with plastic inserts.
- Pros: Versatile, easy to reconfigure.
- Cons: Higher cost, may loosen over time.
3. Roller Side Guides
- Description: Small rollers or wheels mounted vertically along the rail to reduce friction.
- Use Case: Fragile loads (e.g., electronics, glass) or high-speed conveyors.
- Height: 2"–6".
- Material: Steel frame with plastic or urethane rollers.
- Pros: Minimizes damage to delicate items.
- Cons: More expensive, requires roller maintenance.
4. Channel Side Rails
- Description: U-shaped or C-shaped channels that cradle loads.
- Use Case: Small or unstable items (e.g., loose parts, narrow totes).
- Height/Width: 1"–4" high, 1"–2" wide.
- Material: Steel, aluminum, or plastic.
- Pros: Secure containment.
- Cons: Limited to specific load sizes.
5. Flared or Angled Side Rails
- Description: Wider at the top (e.g., funnel-shaped) to guide misaligned loads back to center.
- Use Case: Curved conveyors, inclines, or high-speed systems.
- Height: 2"–8".
- Material: Steel or aluminum.
- Pros: Corrects misalignment.
- Cons: Bulkier, higher cost.
6. Custom Side Rails
- Description: Tailored for unique loads or environments (e.g., food-grade, high-impact).
- Use Case: Specialized applications (e.g., chemical plants, cold storage).
- Material: Stainless steel, reinforced plastic, or coated steel.
- Pros: Perfect fit for specific needs.
- Cons: Expensive, longer lead times.
Design Considerations for Side Rails
1. Height
- Match to load height and stability:
- Low (1"–2"): Small, stable boxes or totes.
- Medium (2"–4"): Standard boxes, light pallets.
- High (4"–8"): Heavy pallets, unstable stacks.
- Ensure clearance for loading/unloading (e.g., forklift access for pallets).
2. Width/Clearance
- Allow 1"–2" clearance per side for smooth flow (e.g., 12" wide box needs 14"–16" between rails).
- Adjustable rails accommodate varying widths.
3. Material
- Steel: Durable, cost-effective; powder-coated or galvanized for rust resistance.
- Aluminum: Lightweight, corrosion-resistant; ideal for portability.
- Stainless Steel: Food-grade, washdown, or corrosive environments.
- Plastic/Urethane: Low friction, protects delicate loads.
4. Mounting
- Bolted: Secure, for fixed rails.
- Slotted/Adjustable: Flexible, for variable loads.
- Welded: Permanent, for heavy-duty systems.
5. Load Dynamics
- Curves: Use flared or roller guides to handle speed differentials.
- Inclines/Declines: Higher rails (e.g., 4"–6") to prevent tipping.
- Accumulation: Smooth or roller guides to avoid damage during queuing.
6. Safety
- Smooth edges to avoid operator injury or load damage.
- High-visibility coatings (e.g., yellow) for safety zones.
- Ensure rails don't obstruct emergency access.
How to Choose Side Rails for a Roller Conveyor
1. Define Load Requirements
- Size: E.g., 12" x 10" boxes need ~14"–16" rail spacing.
- Weight: Heavy pallets (1,000 lbs+) need taller, stronger rails (4"–6").
- Stability: Unstable loads (e.g., stacked boxes) require higher or flared rails.
2. Assess Conveyor Type
- Gravity: Fixed or adjustable rails for simple guidance.
- Powered/Chain-Driven: Adjustable or roller guides for high-speed or accumulation.
- Curved: Flared or roller guides to manage load shifts.
- Pallet: High, sturdy rails (4"–8") for heavy loads.
3. Consider Environment
- Dry/Indoor: Steel or aluminum rails.
- Washdown/Food-Grade: Stainless steel or plastic.
- Corrosive/Outdoor: Galvanized steel or aluminum.
4. Evaluate Adjustability
- Fixed rails for consistent loads; adjustable for mixed sizes.
- Roller guides for delicate or high-speed applications.
5. Check Compatibility
- Ensure rail mounting fits conveyor frame (e.g., bolt holes, slot spacing).
- Verify height doesn't interfere with other components (e.g., sensors, motors).
6. Budget and Maintenance
- Steel rails: Cheapest ($5–$20/ft).
- Stainless steel: More expensive ($10–$50/ft).
- Roller guides: Highest cost ($20–$100/ft).
- Maintenance: Inspect for dents, rust, or loose bolts quarterly.
Pricing for Side Rails
Fixed Steel Rails:
- 1"–2" high: $5–$10 per foot.
- 4"–6" high: $10–$20 per foot.
- Example: 10' of 4" steel rails ≈ $100–$200.
Fixed Aluminum Rails:
- 2"–4" high: $8–$15 per foot.
- Example: 10' of 2" aluminum ≈ $80–$150.
Stainless Steel Rails:
- 2"–4" high: $15–$50 per foot.
- Example: 10' of 4" stainless ≈ $150–$500.
Adjustable Rails:
- Steel: $10–$25 per foot.
- Aluminum: $15–$30 per foot.
Roller Side Guides:
- Plastic/urethane rollers: $20–$100 per foot.
- Example: 10' of roller guides ≈ $200–$1,000.
Flared/Angled Rails:
- Steel: $15–$30 per foot.
- Mounting Brackets/Clamps: $5–$20 each (4–8 needed per 10').
Installation and Maintenance Tips
Installation:
- Bolt or clamp rails to conveyor frame, ensuring alignment with roller surface.
- Space rails 1"–2" wider than load for clearance.
- Use adjustable brackets for flexibility.
Maintenance:
- Inspect quarterly for dents, rust, or loose bolts.
- Clean stainless steel rails in washdown environments to prevent contamination.
- Replace bent or damaged rails to avoid load jams.
- Spare Parts: Stock 10'–20' of rails per conveyor to cover wear or impact damage.
Example Selection
- Scenario: A 15' chain-driven roller conveyor for 1,000-lb pallets (48" x 40").
- Conveyor Specs: 54" wide, 2.5" steel rollers, #50 chain.
- Side Rail Needs:
- Type: Fixed steel, 4" high for pallet stability.
- Spacing: 50" between rails (48" pallet + 2" clearance).
- Length: 15' per side (30' total).
- Material: Galvanized steel (indoor warehouse).
- Cost: 30' × $15/ft = $450.
- Source: Inbelts.
- Spare Parts: Stock 10' extra rail ($150) for replacements.
Side rails for roller conveyors ensure load alignment and safety, with types ranging from fixed steel ($5–$20/ft) to adjustable roller guides ($20–$100/ft). Selection depends on load size, conveyor type, and environment. If you need a specific rail type, pricing for a particular conveyor, or design details, share your conveyor specs (e.g., width, load, type), and I'll refine the response!
Leave Me Your Requirement!