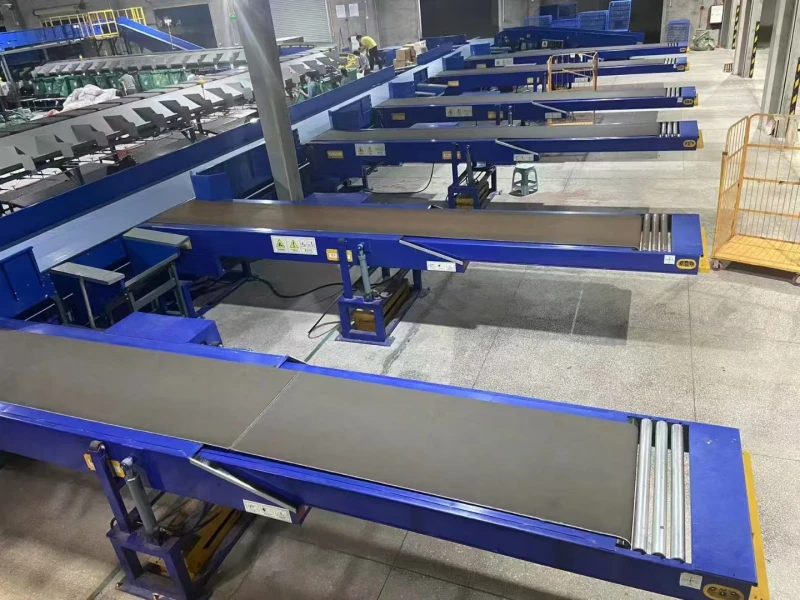
Automatic Sorting Conveyor Systems Enhances Logistics Efficiency
In the logistics industry, the combination of automated sorting systems and conveyors plays a crucial role. Automated sorting systems can quickly and accurately categorize different types of goods, significantly increasing sorting efficiency. Meanwhile, conveyors transport goods from one stage to another, ensuring continuity and efficiency in the logistics process.
Importance of Automated Sorting Conveyor Systems
Statistics show that in a fully automated warehouse system, the efficiency of automated sorting conveyor systems is multiple times higher than manual sorting, with an accuracy rate that greatly exceeds manual operations. For example, in 2018, over 50 billion packages were handled by the national express delivery industry, and with the continued growth in demand, achieving efficient logistics distribution would be challenging without the synergy of automated sorting and conveyors.
An automated sorting system generally consists of control, sorting, conveying devices, and sorting chutes. The control device identifies, receives, and processes sorting signals, instructing the sorting device to categorize items automatically. The sorting device then, based on instructions, changes the direction of goods on the conveyor towards the designated sorting chutes. The conveyor device, composed mainly of conveyor belts or rollers, moves goods through each component and connects various sorting chutes. Finally, sorted goods enter the consolidation area through these chutes. You may get flexible roller conveyors and telescopic belt conveyors from us. These conveyors are widely used in sorting conveying systems, especially telescopic conveyors are used for automatic outbound and inbound storage in warehouses.
Sorting conveyors play a central role in logistics automation. They provide fast, continuous, and stable transport of goods, regardless of weight, increasing transport efficiency while reducing labor costs and intensity. Conveyors can be integrated with other systems, such as storage and packaging, allowing automated handling and transfer of items throughout different stages, enhancing the accuracy and consistency of logistics processes. For instance, in coordination with warehousing, sorting, and packaging systems, conveyors can automatically execute the transport, sorting, and loading of items across stages. Our truck loading conveyors can load and unload container trucks.
In summary, automated sorting and conveyors are essential equipment in the logistics industry. Their coordinated use optimizes efficiency in logistics sorting and transportation, reduces costs, and supports the development of the logistics sector.
Current Technology and Application
Conveyors in automated logistics systems are crucial for fast, continuous, and stable transport, enabling reliable transfer of both light packages and heavy goods, thereby enhancing transport efficiency and reducing labor costs. They can be customized to meet unique business needs and warehouse environments, providing flexible sorting options. For example, an e-commerce company can tailor a conveyor system to suit its warehouse layout and product types, greatly improving logistics efficiency.
Automated control systems enable real-time monitoring and tracking of conveyor processes, increasing transport safety and reliability while enabling prompt issue detection. If a problem occurs with the items on the conveyor, the control system can trigger an alert, allowing personnel to address it swiftly. The control system also records transport data, aiding companies in making logistics management decisions.
In sectors such as e-commerce, express delivery, and new retail, the application of automated sorting and conveyor systems has become increasingly common. Solutions have diversified to suit various needs. For example, in e-commerce, automated sorting systems utilize advanced identification and scanning technology to quickly determine package size, weight, and destination, sorting items to specified areas accurately. The conveyor then moves sorted packages to the next stage, facilitating efficient logistics distribution. In the express delivery sector, belt conveyors are widely used for sorting, weighing, security inspection, and warehousing, enhancing efficiency and accuracy. In new retail, automated sorting and conveyor systems are custom-designed to accommodate diverse logistics needs.
Key Factors for Optimization in Coordination
1. Enhancing Sorting Speed and Accuracy
Automated sorting equipment integrated with conveyors significantly reduces the required workforce, enhancing sorting efficiency. For example, in automated express sorting lines, advanced mechanical, electronic, and computing technologies are utilized to swiftly sort and classify packages. Vision recognition technology, the core of automated sorting, employs high-resolution cameras and image processing systems to quickly and accurately identify barcodes on packages, matching them with database information for automatic sorting. Conveyors then transport sorted packages to the next stage, greatly improving sorting speed and accuracy.
2. Evolution of Sorting and Conveying Technology
While the fundamental principles of traditional sorting systems remain, continuous innovation in technology has advanced intelligence. For example, suppliers have developed unique technologies based on industry needs and application scenarios. The modular conveyor platform (MCP) introduced by Interroll allows for maximum variety in product specifications with minimal components, catering to various customer needs. With standardized parts and interfaces, internal components are interchangeable, reducing production and maintenance costs.
3. Adapting to Different Scenarios
Selecting conveyors requires consideration of future customer demands, space constraints, and downtime impact. Material characteristics and environmental conditions, such as weight, surface features, packaging, size, and speed, influence conveyor selection. Conveyor system environments, including extreme temperatures, lighting, and air conditioning, also affect decisions. Maintenance and associated costs must be factored into equipment selection.
Logistics robots are more adaptable than conveyors for rapidly growing and complex sorting needs, with advantages in space utilization and safety. Smart sorting robots can automatically sort, pack, and seal items as per user requirements and site conditions. With large-scale scheduling capabilities and intelligent path planning, robots work continuously, are lightweight, efficient, and save labor. For example, a major e-commerce logistics center that introduced intelligent sorting robots saw daily package handling and sorting accuracy rates increase dramatically.
Key Technical Aspects in Coordination
1. Control Requirements
Traditional automated sorting conveyor systems, due to lower technological levels, were limited in sorting variety and precision. Today, technologies such as PLC, position control, and pneumatic technology have enabled automated material sorting, enhancing productivity. For example, the THFCL-1 material sorting teaching model incorporates these technologies and can be applied in production processes requiring repetitive sorting of specific features.
2. Components of an Automated Sorting Transmission System
An automated sorting system generally comprises synchronized feeder loading devices, recognition and control systems, mechanical sorting mechanisms, and information processing systems. Synchronization ensures smooth, orderly entry into the sorting system. Recognition and control systems read material information and issue sorting commands, while mechanical mechanisms execute actions, and information processing collects and analyzes data for logistics management decisions.
3. Automated Sorting and Conveying Equipment
Automated sorting technology is crucial for cost-effective logistics management. For example, the Inbelts intelligent sorting system series achieves 2,500 items per hour, 2.5-8 times manual efficiency, with broad sorting capabilities for packages of various shapes and sizes. The system allows modular window configuration for flexible addition, improving space efficiency.
Future Development Trends
1. Increased Intelligence
With the integration of AI, big data, and IoT, sorting and conveyor systems will become increasingly intelligent. IoT enables real-time monitoring and remote control for stable operation and troubleshooting, while big data analysis identifies bottlenecks in logistics for targeted improvements. AI algorithms can optimize sorting paths, raising efficiency by over 30% and reducing errors to below 0.1%.
2. Green Development
In line with global carbon goals, automated systems will adopt more energy-efficient motors and control systems, reducing consumption by over 20%.
3. Growing Customization
Logistics industry growth is driving demand for custom automated systems. Manufacturers will provide solutions tailored to clients’ needs, improving equipment suitability and competitiveness.
4. International Expansion
Domestic manufacturers are expanding globally, establishing production and sales networks in Southeast Asia, Europe, etc. In turn, domestic companies are incorporating international technologies to enhance competitiveness.
Leave Me Your Requirement!